品質管理
品質管理の概説
品質管理の定義
品質管理とは、設計図および仕様書に示された形状と規格を十分満足するような土木構造物を最も経済的に作るための、その工事のすべての段階における品質の管理体系であります。工事の問題点を把握するとともにその改善方法を見出すことにより、構造物の欠陥を未然に防ぎ、工事に対する信頼性を増すものです。
日本産業規格JISZ8101-1981(1999年に廃止され、ISO9000ファミリー(またはシリーズ)に統合)では、品質管理を「買手の要求に合った品質の品物またはサービスを経済的に作り出すための手段の体系」と定義しています。考え方は以下のとおりです。
- 顧客に提供する品物やサービスが顧客の要求する品質、価格、納期になっていること
- 品物やサービスなどを、各職場や部署で他社より安く早く効率よく提供できること
- それらを実行するために、固有技術だけではなく統計を利用した管理技術を全社的に行うこと
また、品質管理を効果的に実施するためには、市場調査、研究、製品の企画、開発、設計、生産準備、購買、外注、製造、検査、出荷、販売およびアフターサービス、財務・経理、人事、総務などの企業の全部門で品質管理活動を進めていく必要があります。
品質管理の範囲では、「狭義の品質管理」と「広義の品質管理」があり、以下のとおり定義されています。
- 狭義の品質管理とは、製品のみの品質管理活動を行う顧客に提供する活動である。
- 広義の品質管理とは、顧客や社会の要求を満たし、ニーズに合った製品やサービスを作って提供するための活動「TQM」(総合的品質管理)や「TQC」(全社的品質管理)である。
なお、本書で取り扱う品質管理は、主として統計的手法を利用した、工事の施工段階での品質向上のための手法としての狭義の品質管理であり、統計的品質管理に関するものである。
品質管理に関するISOの規格体系
ISO規格とは、国際標準化機構(ISO)が定めている国際規格のことです。現在、建設業で取り組まれている主なものとしては、ISO9000ファミリー(品質マネジメントシステム)とISO14000ファミリー(またはシリーズ)(環境マネジメントシステム)の2種類があります。ISO規格の認証取得は、組織(受注者)が、国際的にも国内的にも顧客(発注者)の要求事項や社会的要求事項、組織の要求事項に適合しうる能力を保持していることを第三者である審査登録機関により証明される ことにあります。
日本では公益財団法人日本適合性認定協会が「認定機関」としてISOに加盟しており、日本にある複数の審査登録機関を審査し認定する役割を負っています。
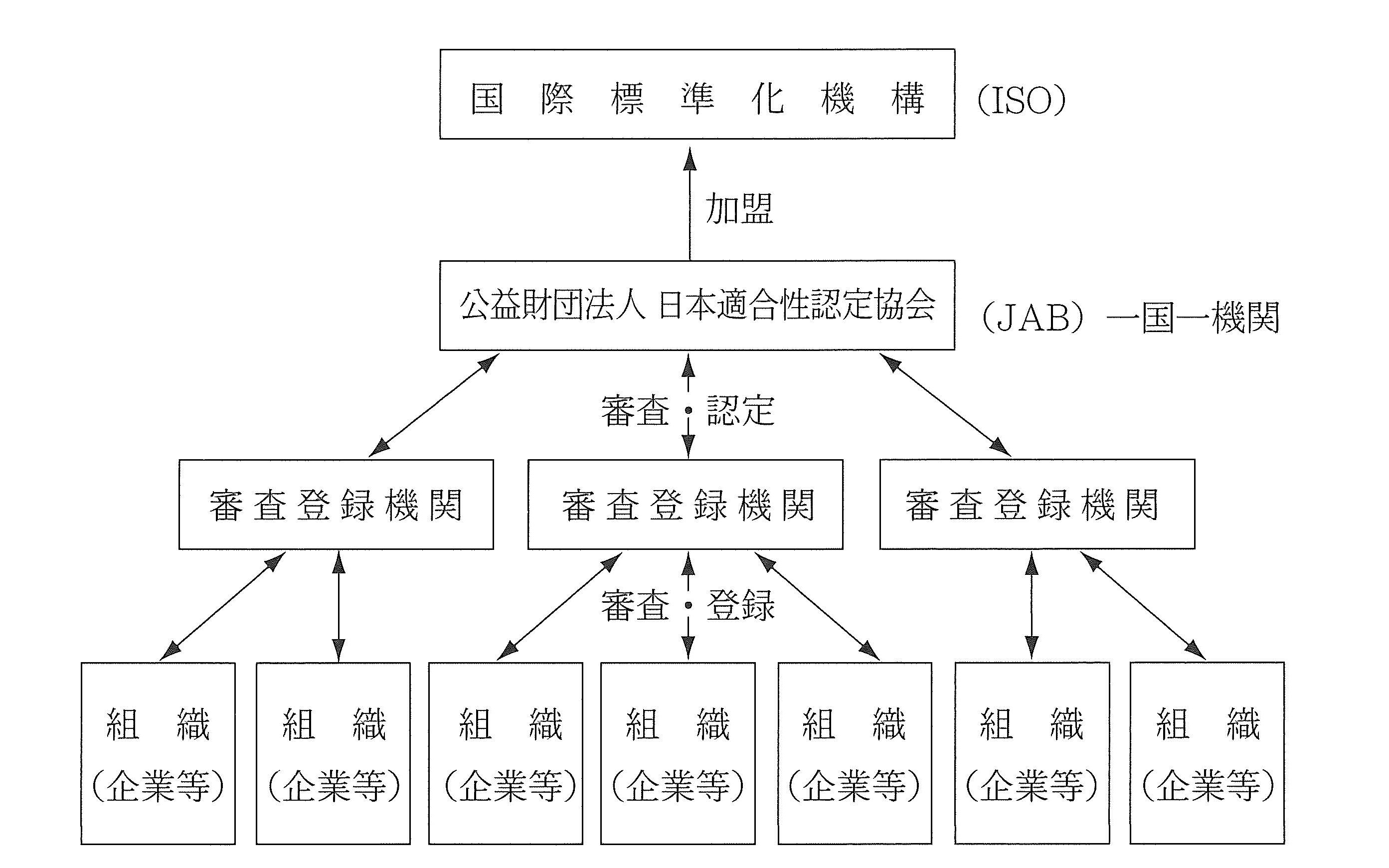
図-1:ISOマネジメントシステム審査登録の仕組み
ISO9000ファミリー
組織(企業等)が顧客の要求に応えるために、要求に関する情報を吸い上げ(インプット)、製品やサービスに反映して提供する(アウトプット)必要がある。このインプットをアウトプットに変換することを「プロセス」と呼んでいる。絶えず変化する顧客の要求に応えるために、プロセスを継続的に改善していくことを品質マネジメントシステムという。品質マネジメントシステムは、顧客の信頼と満足を得ることを目標に、品質方針や品質目標を設定して、これらを達成するために組織を適切に指揮·管理する仕組みのことであり、組織の構造、責任区分、業務手順、工程、経営資源など、受注·生産·販売活動に関わるすべてを指す。品質マネジメントシステムの基本·用語定義、要求事項、組織のパフォーマンス改善、マネジメントシステムの監査について定めているのが、ISO9000ファミリーである。
1 ISO9000ファミリーの全体構成
ISO9000ファミリーは、次の4つのコア規格から構成されており(図-2)、これらをひとつのセットとして活用することにより最大限のメリットが引き出せるようになっている。
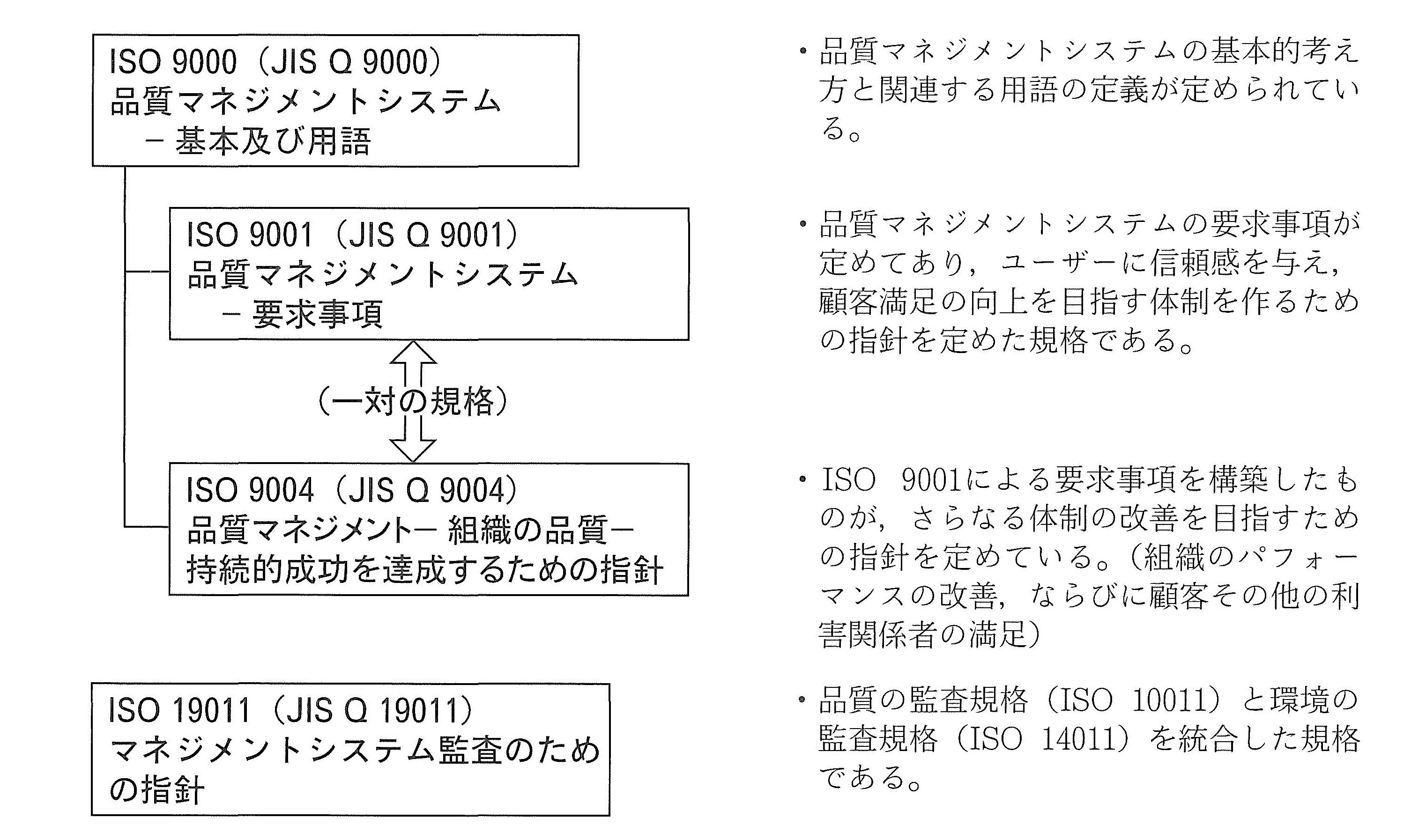
図-2:ISO 9000ファミリーの構成図
2 ISO9000ファミリーの特徴
- あらゆる業種および規模への適用可能性の向上
- あらゆる産業および規模の組織にも適用できるような用語の選択、要求事項の記述がされている。
- 品質マネジメントの原則の採用
- 品質マネジメントの原則は『3 品質マネジメントの原則』に示す7個である。これらの原則を理解し、実行することで品質マネジメントの目的を達成することができる。
- プロセスアプローチの採用
- 品質マネジメントシステムの構築、実施、改善においてプロセスを明確にし、一連のプロセスシステムとして適用することを採用する。
- 顧客志向の重視
- 顧客満足、顧客のニーズの把握、要求事項の理解、顧客とのコミュニケーションなど、顧客の重要性を強調する。
- 継続的改善の導入
- 品質マネジメントシステムの運営において、継続的な改善を全面的に 導入している。
- 資源の運用管理の充実
- 品質マネジメントにおける資源(人、設備、資材、資金、技術、情報、作業環境等)の重要性を認識し、記述を充実する。
- トップマネジメントの責任および役割の拡大ならびに明確化
- 組織運営におけるトップマネジメント(経営者)の役割の重要性を認識し、トップマネジメントが実施すべき事項を明確に規定する。
3 品質マネジメントの原則
- 顧客重視
- 品質マネジメントのもっとも重視している視点は、顧客の要求を満たして顧客の期待を上回る努力をすることである。
- リーダーシップ
- すべての階層でのリーダーは、目的と方向性を一致させ、組織の目標を達成させることに人々が参画する状況を構築する。
- 人々の積極的参加
- すべての人々が力量をもち、権限を与えられ、参画することが、組織にとって不可欠である。組織全体にわたって、人々が参画するとき組織の価値創造能力は高まる。
- プロセスアプローチ
- 活動が、一連のシステムとして機能し、相互に関連するプロセス(インプットをアウトプットに変換することを可能にするために経営資源を使って運営管理する活動)が理解され運用されたときに、一貫性があり予測可能な結果が、より効果的で効率的に達成される。
- 改善
- 成功している組織は、継続的な改善を重視している。
- 客観的事実に基づく意思決定
- データ、情報の分析および評価に基づく決定は、望ましい結果を生み出す可能性を高める。
- 関係性管理
- 継続的な成功のためには、組織は協力会社のような、利害関係者との関係をうまく運営しなければならない。
4 プロセスおよびプロセスアプローチ(ISO9001)
プロセスの特色
- 何を目的として、どのような活動や作業をどの範囲で行い、どのような結果(アウトプット)を得るかを明確にできる。
- P-D-C-Aサイクルがすべてのプロセスに適用可能。サイクルを回すことにより、継続的改善が実施される(図-3)。
P-D-C-Aサイクルとは、
- 顧客要求事項および組織の方針に従った結果を出すために必要な目標およびプロセスを確立する。(Plan)
- プロセスを実行する。ここでは、その有効性についても検討する。(Do)
- プロセスおよび製品を、方針、目標および製品に対する要求事項に照らして監視し、測定し、結果を報告する。(Check)
- プロセスのパフォーマンスを継続的に改善するための処置をとる。(Act)
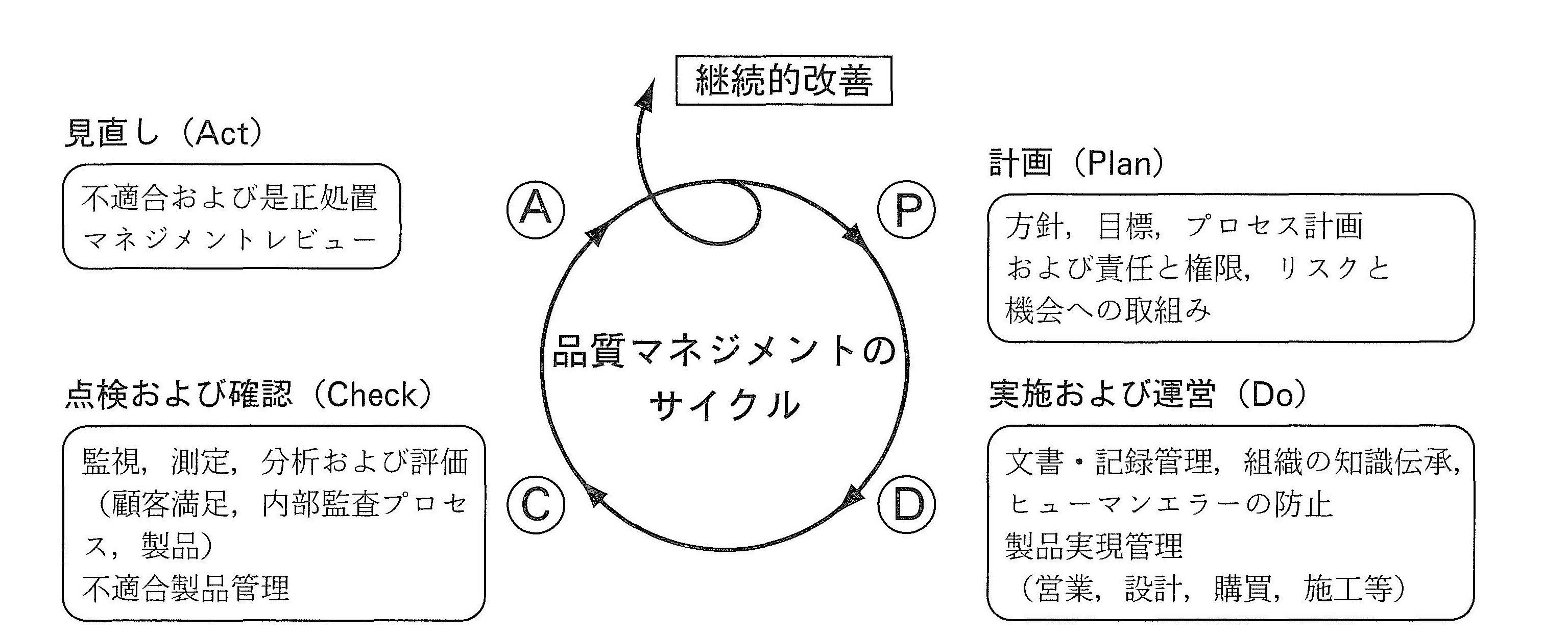
図-3:品質マネジメン卜のサイクル
プロセスアプローチ
- プロセスアプローチとは、これらのプロセスを明確にし、その相互作用を把握することによって全体を管理すること。
- プロセスアプローチの利点は、システム内の個々のプロセス間のつながり、およびそれらの組合せと相互作用を継続的に管理することができることである(図4.4)。また、プロセスアプローチを用いることにより、システム全体の活動が整合性の取れた、実際的な流れとして管理することができる。
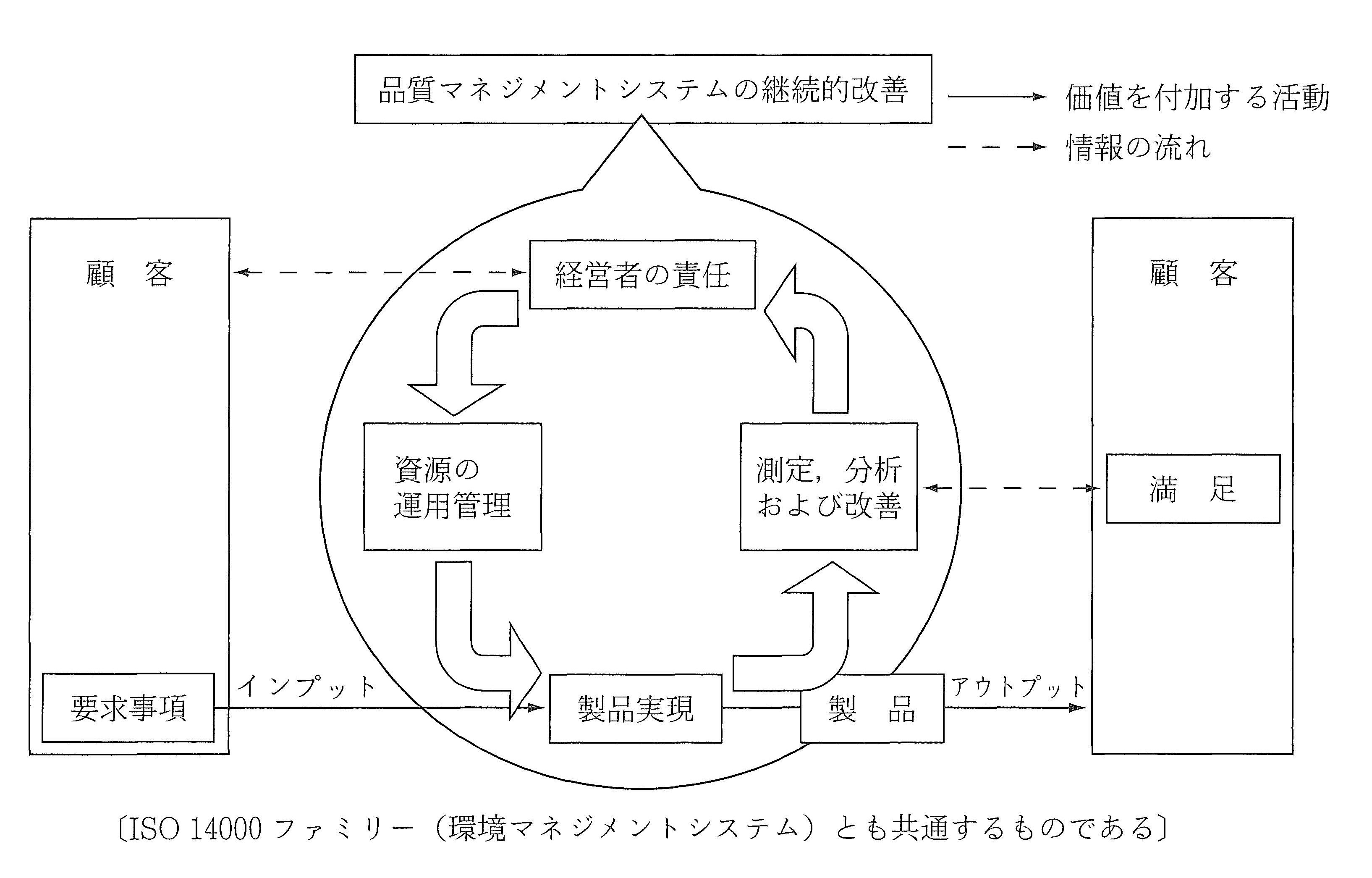
図-4:プロセスに基づいた品質マネジメン卜システムのモデル図
5 ISO9001認証取得の活用
ISO規格の認証取得は、組織が顧客の要求事項に適合し得る能力があることを第三者である審査登録機関により証明されることにある。したがって、工事発注者は、受注者の持つ要求事項を満足させる能力の実証および評価に活用することができる。 国土交通省および一部地方自治体発注のISO9001活用工事では、ISO9001認証取得した工事受注者の品質マネジメントシステムに基づく自主的な品質管理業務を活用して、監督業務の一部を工事受注者の検査記録の確認に置き換えることで、工事の品質確保と効率化が図られている。
ISO14000ファミリー
ISO14000ファミリーは、環境保全のための規制値や基準値を定めるものではなく、組織が自主的に環境方針を定め、それを実行していくための環境マネジメントシステムおよびシステムを支援する様々な手法を規定した一連の規格である(図-5)。
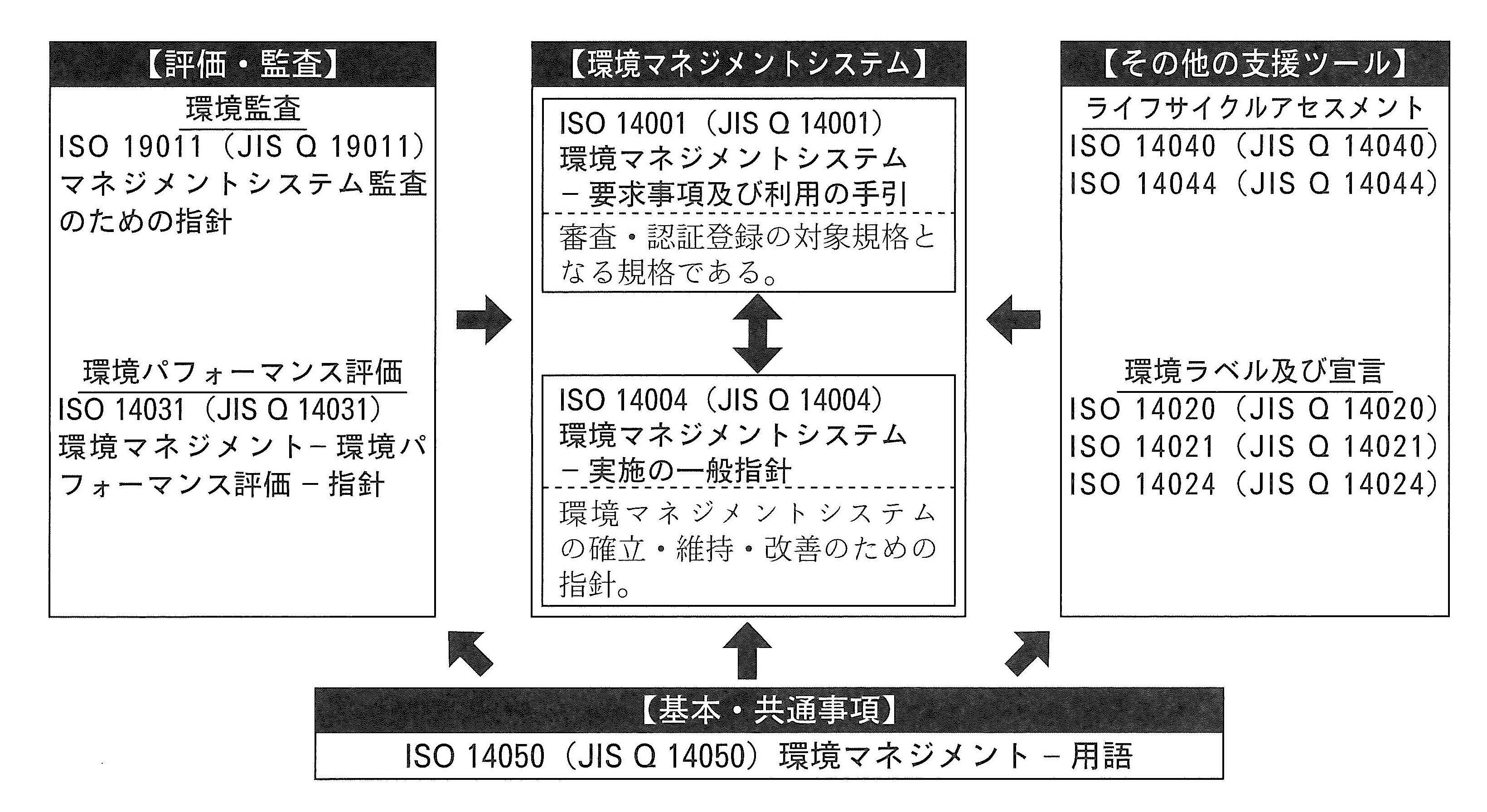
図-5:ISO 14000ファミリーの構成図
ISO9000ファミリーとISO14000ファミリーの比較
ISO9000ファミリーとISO14000ファミリーはいずれもマネジメントシステムと呼ばれる組織の経営運用に関わる仕組みや活用に関する規格であり、各々の要求事項には共通するところが多い。
ただし、各々の規格はその目的が違い、ISO9000ファミリーは「顧客ニーズ」に対応するために組織内に品質マネジメントシステムを構築し、それを実施·運用することによって顧客が満足する製品やサービスを提供するものであるが、ISO14000ファミリーは「広い利害関係者のニーズや環境保護に対する社会の新しいニーズ」に対応するために組織内に環境マネジメントシステ35 ムを構築し、それを実施·運用することで環境負荷の低減を図ることが目的である。ISO9000ファミリーおよびISO14000ファミリーの中で中心となる規格が、ISO9001およびISO14001である。
品質管理の方法
品質管理の目標
土木工事における品質管理の直接の目標は、次の2点を確認することです。
- 構造物が規格を満足していること。
- 工程が安定していること(工程とは、工期工程とは異なり、品質が作り出される過程をいう)。
土木工事の品質管理においては、発注者が要求した規格や品質を十分なゆとりをもって満足させながら、土木構造物を最も経済的に造られなければなりません。したがって、まず、検査した個々のデータがゆとりを持って規格値を満足することが必要です。ただし、全体として規格値に対してゆとりがありすぎる場合、その原因が必要以上に高級な材料の使用であったり、必要以上に丁寧な施工であれば不経済な工事となり、適切とはいえません。次に、個々のデータは規格値を満足しても、そのバラツキが異常に大きい場合、工程が安定しているとはいえず、検査しなかった部分の品質に対する信頼性が低下するので、工程が安定している必要があります。このようなことから、上記2点を適切な範囲で同時に満足させることが品質管理の目標となります。なお、一般に、構造物の品質を確認する方法として、ヒストグラムや工程能力図が用いられ、工程の安定性を確認する方法として管理図が用いられます。
工程能力図
- 特徴
- 横軸に時間や測定No.、縦軸に品質特性値をとり、規格値を示 す線を記入して、データを時間の順序に打点した図である。
- 規格値で管理する。
- 目的・利点
- 時間的な品質変動や傾向がわかる。
- 規格値との関係がわかる。
- 欠点:
- 統計的手法が使われていないため、工程の異常は判断できない。
ヒストグラム
- 特徴
- 横軸に品質特性値、縦軸に度数をとり、規格値を示す線を記入して、品質特性の分布状態を表した度数分布図である。
- 規格値で管理する。
- 目的・利点
- 分布の状態から規格値、中心位置(平均値)の関係がわかる。
- 工程の状態を把握できる。
- 欠点
- 時間的変化や変動の様子がわからない。
管理図
- 特徴
- 品質データを統計的に処理し平均値やバラツキの範囲などに対する管理限界線を求めて記入し、その後のデータの平均値やバラツキの範囲を打点した図である。
- 管理限界線で管理する。
- 目的・利点
- 工程が安定しているかどうかを評価する。
- 欠点
- 時間的変化や変動の様子がわからない。
- 規格値との関係はわからない。
品質管理の手順
品質管理の手順として、工程能力図、ヒストグラムや管理図の作成に入る前に、品質特性の選定、特性に関する品質標準の設定、品質標準を守るための作業標準の決定などについて、十分検討することが必要です。
- 手順1:品質特性の選定
- 管理しようとする品質特性を選定する。一般的な品質特性の例はこちらを参照。
- 手順2:品質標準の設定
- 選んだ品質特性に関する品質標準を設定する。品質標準は、設計図·仕様書に定められた規格をゆとりをもって満足するための施工管理の目安を設定するものである。実施可能な値でなければならず、一般的には、平均値とバラツキの幅で設定する。
- 手順3:作業標準の決定
- 品質標準を満足させるための作業標準(作業の方法)を決定する。品質標準を満足する構造物を施工するために、作業ごとに用いる材料、作業手順、作業方法等をできるだけ詳細に決める。
- 手順4:データ採取
- 作業標準に従って施工し、一定の期間、データを採る。試験方法および検査方法の標準を定める。
- 手順5:分析確認
- 処理: 各データが十分ゆとりをもって品質規格を満足しているかどうかを工程能力図、ヒストグラム等により確かめたのち、管理図をつくり、工程が安定しているかどうかを確かめる。
- 手順6:作業方 法の見直し
- 施工の途中で管理図により工程に異常が生じたと判定された場合、原因を追求し、再発しないよう作業方法を見直すなどの処置をとる。
- 手順7:作業の継続
- 処理: 引き続き作業を続け、データを監視しながら、前回と同程度の期間(例えば1か月)、あるいは、データが一定の数(例えば20点)に達したら、手順5以下を繰り返す。
この手順は、具体的に品質管理を進めるときに実行していく順序であるが、手順5から7における統計的手法として、工程能力図、 ヒストグラムや管理図などが用いられる。
品質特性の選定
品質管理の第一歩は、構造物に要求されている品質・規 格(設計品質)を正しく把握することです。設計品質は、一般に、設計図書、特に仕様書に示されていますが、それらを満足させるためには、何を具体的な品質管理の対象項目とするかをあらかじめ整理しておく必要があります。品質管理におけるこのような具体的な対象項目を品質特性といいます。(管理特性、管理項目と呼ぶこともあります)
なお、品質管理の対象とする品質特性は、次のようなものであることが望ましいです。
- 工程(作業)の状態を総合的に表すものであること。
- 品質に重要な影響を及ぼすものであること。
- 代用特性(真の品質特性と密接な関係があり、その代わりとなり得る品質特性)または、工程要因を品質特性とする場合は、真の品質特性との関係が明らかなものであること。
- 測定しやすいものであること。
- 工程に対して処置がとりやすいものであること。
- 早期に結果が得られるものであること。
- できるだけ工程の初期段階において測定できるものであること。
工程要因を品質特性とする場合とは、例えば、土の締固め管理の基準には乾燥密度などを 規定する品質規定方式と締固め機械や転圧回数などの施工方法を基準とする工法規定方式がありますが、工法規定方式を用いる場合がこれに相当します。
品質標準の設定
品質標準とは、施工に際して実現しようとする品質の目標であり、従来は設計品質そのものを採用している場合が多 いですが、品質特性のバラツキが大きい場合は、設計品質を満足しないものが出てくるおそれがあります。したがって、品質標準は設計品質に対して余裕のある設定としなければなりませんが、統計的理論だけから合理的で妥当な品質標準を設定すると困難なことが多くなります。
そこで、土木工事においては、過去の実績や試験施工などをもとに当初の概略標準を定め、施工の過程に応じて結果をフィードバックしながら、標準を改訂していく方法をとる場合が多いです。
作業標準の決定
品質標準の設定とともに、この品質を実現するための作業の方法、使用する資機材などをできるだけ具体的かつ詳細に作業標準として決定し、作業者に周知徹底しておく必要があります。
この作業標準は、過去に施工した同種条件の施工実績や経験を参考にするか、または品質標準を設定する場合と同様に、事前の試験施工や実験の結果などを参考にして決定します。なお、作業標準を決定するときには、次の点に留意する必要があります。
- 先手を打った管理が行えるような作業標準にすること。
- 最終品質に重大な影響を及ぼす要因については、できるだけ詳細かつ具体的に作業標準を決めること。
- 工程に異常が発生した場合は、誰が、何を、どこまでやるべきかを具体的に作業標準として決めておくこと。
- 作業標準の間で矛盾がないこと。
- 作業標準は明文化しておき、技術の蓄積を図るよう心がけること。
先手を打った管理とは、例えば、打設前の型枠寸法のチェックやコンクリートの現場搬入時のスランプのチェックにより、粗悪なコンクリート打設をあらかじめ防止するような手順を作業標準の中に組み込むことをいいます。
工程能力図
工程能力図の概要
工程能力図は、時間的な品質変動の関係を表したものであり、得られた品質特性値(データ)が規格値を満足しているかどうかのチェックに用いられる連続的な表示方法です。工程能力図により、規格値に対するデータの変動の様子を連続的に把握することができますが、統計的な考え方が使われていないため、これだけから直ちに工程上異常があるかどうかを判断することはできません。
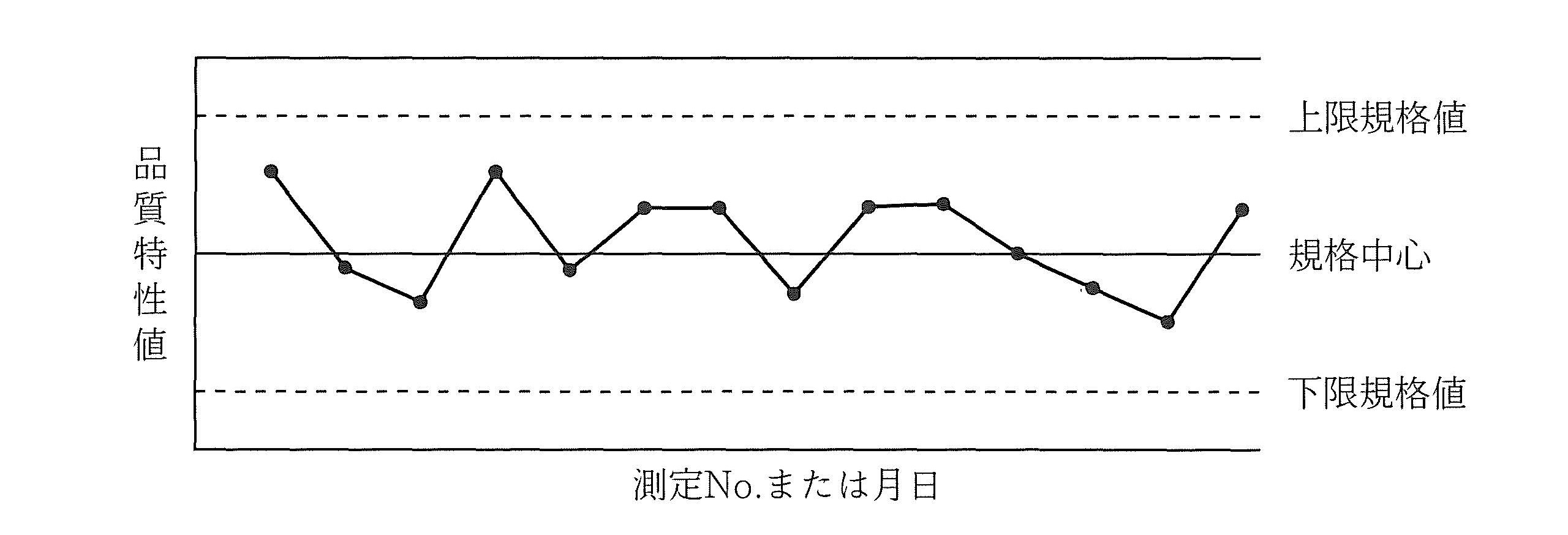
図-6:工程能力図
なお、工程とは、工期工程とは異なり、品質が作り出される過程を指します。また、工程能力図は、規格の管理に使われるものですが、管理図と混同されやすいので注意が必要です(工程能力図は、データを規格値と対比するために用いられるものです。一方、管理図は、データが統計的手法により定めた管理限界線の内側に入っているかどうかを調べるために用い られるものです)。
工程能力図の作り方
工程能力図は、調べようとする対象の集団を区間割(工区等)し、合理的な群にして、各群の中で時間順序に従って、データを記入して作成します。
工程能力図は、グラフ用紙の横軸に測定No.または月日を、縦軸に品質特性値を目盛り、上下限規格値を示す線を引きます。各データは、そのまま測定した順序に1点ずつ打点し、各点を実線で結びます。
ヒストグラム
ヒストグラムの概要
ヒストグラムは、データの分布状態を知るために多く用いられる統計的手法であります。横軸に品質特性値(データ)の存在する範囲をいくつかの区間に分け、それぞれの区間に入るデータの数を度数として縦軸にとった図であります。図が柱状になっていることから、柱状図(度数分布図)とも呼ばれます。
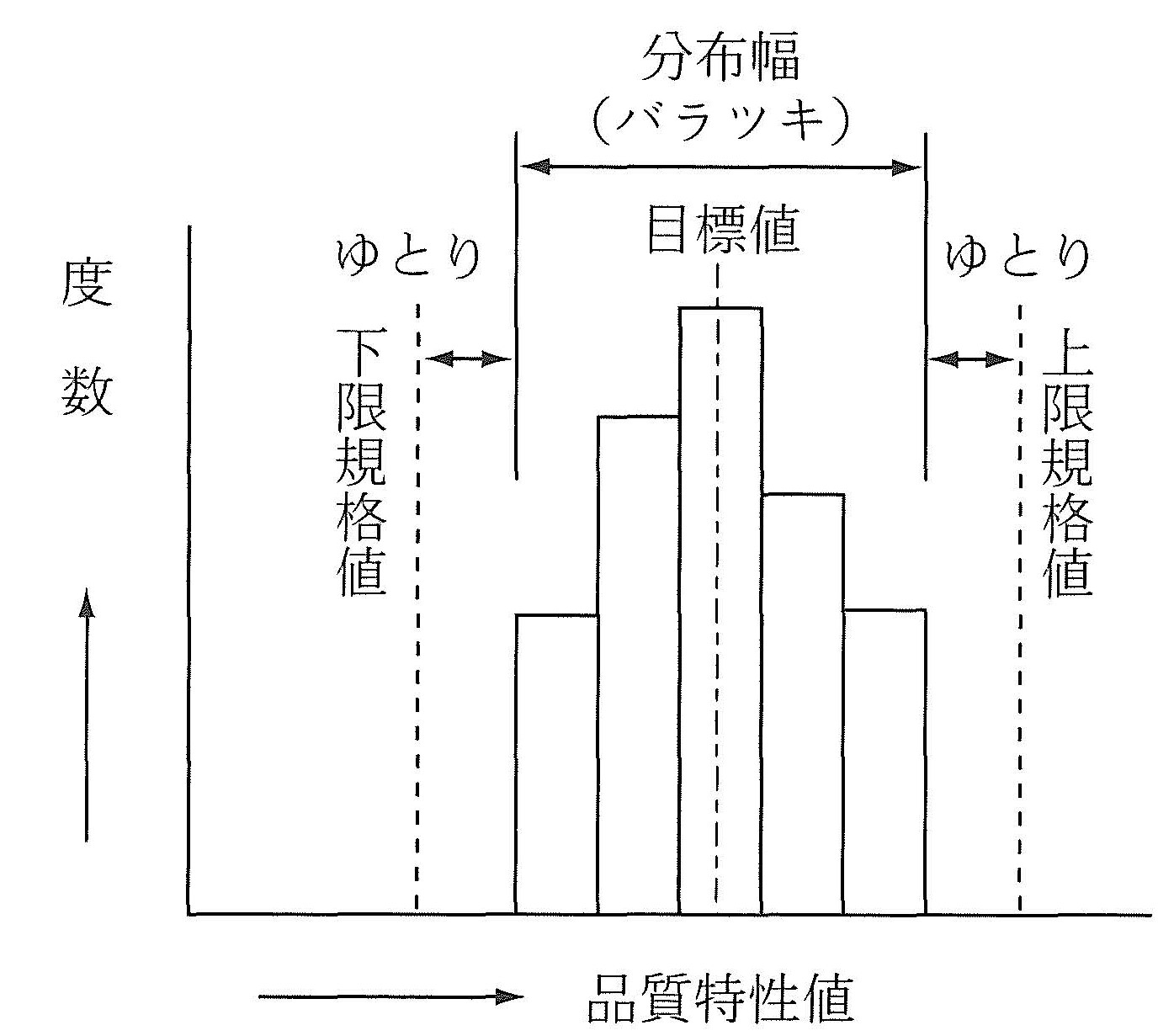
図-7:ヒストグラム
通常、ヒストグラムの中に品質管理の基準となる品質特性値の規格値を記 入し、ヒストグラムの分布の平均値と中心値(目標値)および規格値を比較するなどして、規則性、工程の状態を把握することができます。ただし、ヒストグラムでは、個々のデータの時間的変化や変動の様子はわかりません。ヒストグラムからわかることは、次のとおりです。
- 分布の形状
- 分布の中心位置(平均値)と中心値(目標値)との関係
- 分布の広がり
- 飛び離れたデータの有無
- 規格値との関係
ヒストグラムの作り方
ヒストグラムを作る一般的手順は、以下のとおりです。また、同時にヒストグラムの作り方の例を示します。
手順1. 最近のデータをできるだけ多く集めます。
列 | 1列 | 2列 | 3列 | 4列 | 5列 |
---|---|---|---|---|---|
1 | 22 | 22 | 23 | 23 | 24 |
2 | 24 | 23 | 23 | 23 | 22 |
3 | 22 | 22 | 22 | 23 | 23 |
4 | 22 | 23 | 22 | 21 | 25 |
5 | 23 | 23 | 22 | 25 | 23 |
6 | 23 | 21 | 24 | 19 | 21 |
7 | 23 | 23 | 22 | 23 | 21 |
8 | 21 | 23 | 22 | 21 | 24 |
9 | 25 | 24 | 27 | 23 |
手順2. データの中から最大値、最小値を求めます。
ここでは、最大値、最小値 となります。
列 | 1列 | 2列 | 3列 | 4 列 | 5列 |
---|---|---|---|---|---|
25 | 24 | 27 | 25 | 25 | |
21 | 21 | 22 | 19 | 21 |
手順3. 全体の範囲、を求めます。
ここでは、範囲
手順4. クラス分けする時のクラス幅を決めます。
建設工事の場合、データの数が少ないときは、クラスの数を5~8としてかまいません。
データの数 | クラスの数 |
---|---|
50以下 | 5~8 |
100以内 | 10 |
500程度 | 10~15 |
1,000以上 | 20 |
÷(クラスの数)=
を測定値の位に合わせ、これをクラスの幅とします。
手順5. 、を含むようにクラスの幅で区切り、各クラスを設けます。
このとき、クラスの境界に位置するデータは、測定単位より一桁下の5単位で区切るとよいです。これは、データを分ける場合に、はっきりどのクラスに属するかを決めるためです。
手順6. クラスの中心値(代表値)を求めます。
手順7. データを各クラスに分けて度数分布表を作ります。
このときチェックマークには////を用い、“正”は用いません。なお、このチェックは単純作業で間違いやすいので、2度行う必要があります。
手順8. 横軸に品質特性値、縦軸に度数をとって、ヒストグラムを作ります。
手順9. ヒストグラムに、規格値(上限または下限)を記入します。
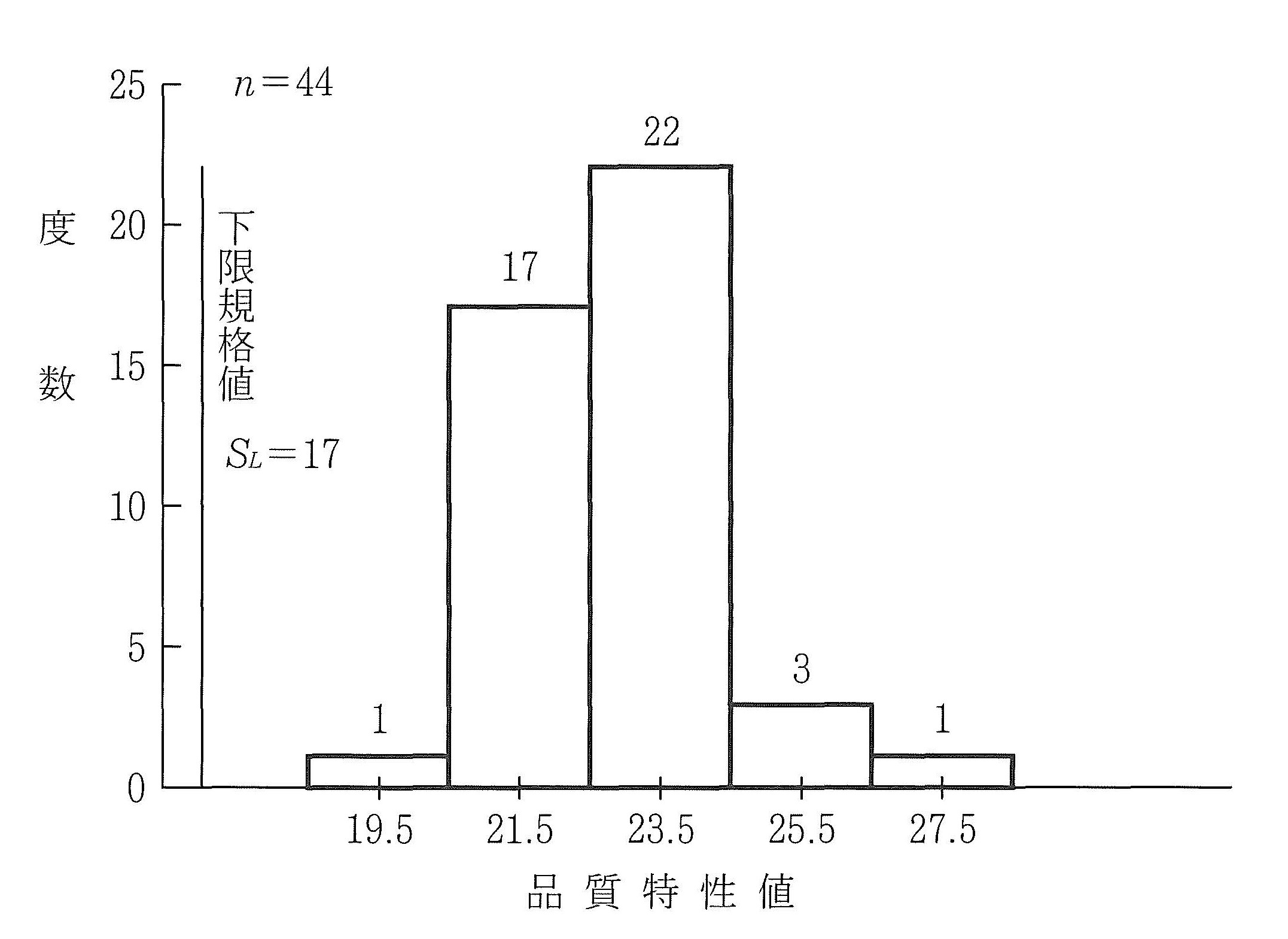
図-8:ヒストグラム完成例
ヒストグラムの見方
分布形状および規格との比較
測定値のヒストグラムは、一般に、中心付近が最も高く、中心から離れるほど低くなる左右対称のつり鐘型を示すことが多いですが、実際には、種々の要因によっていろいろな形状のものが生まれます。
規格や目標値が決まっている場合には、ヒストグラムに規格値(上限、下限)、目標値を線で記入し、ヒストグラムが規格値に対して十分なゆとりをもっておさまっているかどうかを見ます。
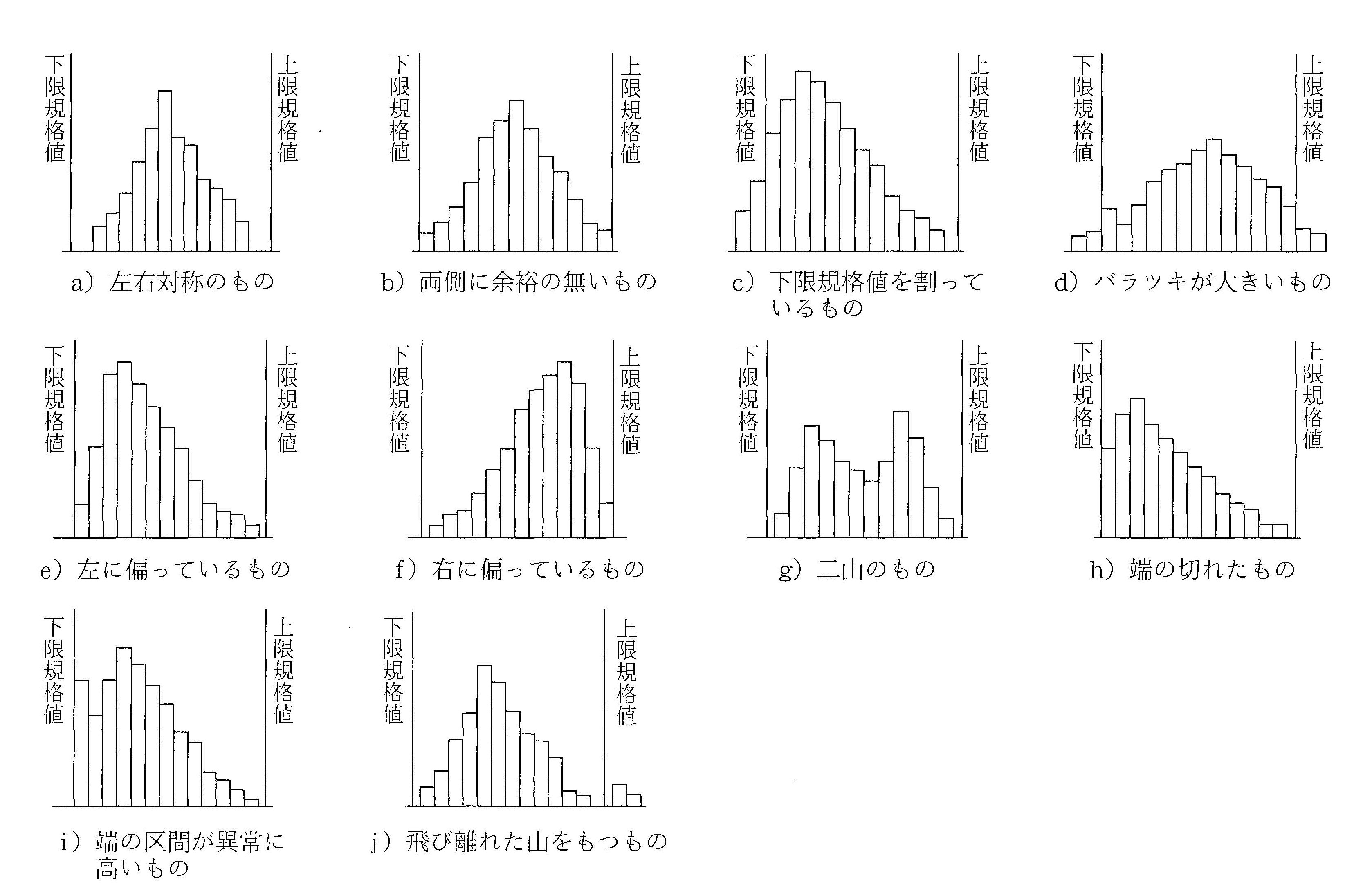
図-9:ヒストグラムの分布形状
これらのヒストグラムの形状と品質管理あるいは工程管理との一般的な関係は、以下のとおりです。
- a)規格値に対するバラツキもよくゆとりもあり、平均値も規格値の中心と一致する。品質管理上の理想的な型。
- b)規格値の範囲内であるが、わずかな工程の変化によって規格値を割るものがでるので、バラツキをもっと小さくするよう品質管理する必要がある。
- c)分布全体が左に寄りすぎ、下限の規格値を割っている。平均値を大きい方にずらし、バラツキを小さくするよう処置する必要がある。
- d)上・下限の規格値をともに割っており、応急措置が必要である。バラツキを小さくするための要因(現状の技術レベルまたは作業標準)を解析し、根本的な対策を採ることが必要である。
- e,f)上 限または下限が規格値などで抑えられた場合で、特定の値以下または以上の値をとることが許されない場合によく現れる形状である。
- g)1つの製品の製作に2つの異なる工程(2台の機械や2種類の原材料)を用いた場合に現れやすい分布であり、平均値の異なる2つの分布が混在している。
- h)規格値以下のものを工程の途中で全数取り除いた場合に現れる。
- i)規格値以下のものを手直ししたり、データを偽って報告した場合に現れる。
- j)測定に誤りがあったり、工程に時折異常があった場合に現れる。
留意点
ヒストグラムを見る場合は、以下の点に留意する必要があります。
- 規格値を満足しているかどうか。
- 分布の位置は適当か。
- 分布の幅はどうか。
- 離れ島のように飛び離れたデータはないか。
- 分布の右か左かが、絶壁型となっていないか。
- 分布の山が2つ以上ないか。
なお、ヒストグラムにより品質管理の判定を行う際には、規格値に対するゆとりがどの程度あるかを統計手法により計算して確認しておくことが望ましいです。
品質管理においては、このようにしてヒストグラムを見ながら、品質全体の傾向や規則性をつかみ、不良原因や問題点を追求するとともに、速やかに改善などの是正措置をとる必要があります。このような品質管理を積み重ねることによって、技術上の新しい課題やその改善方法が見出され、施工技術が向上していくことになります。
統計量の計算
ヒストグラムを見ただけでは、分布の幅や中心位置はその概略値しかわかりません。また、いくつかのヒストグラムを比較する場合は、各ヒストグラムの分布の差を正確に表現することが難しいです。
このため、分布の姿としての性質を数量的に表すことができれば、だれもが一致した数値で比較判断することができて便利です。そこで、以下に示すような、各種の統計量が用いられています。
データの中心位置の表し方
平均値
測定値の算術平均。
例えば、測定値が のとき、
メディアン(中央値)
測定値を大きさの順に並べたとき、ちょうど中央にあたる1つの値(奇数個の場合)、または中央の2つの値の算術平均(偶数個の場合)。
測定値が のときは、。
また、測定値が のときは、。
データのばらつきの表し方
範囲(:レンジ)
測定値の最大値と最小値の差。
上の例では、
平方和(:残差平方和)
個々のデータの平均値と各データとの差を二乗したものの和。
上の例では、
分散()
バラツキの程度を見るためには、残差平方和では不便であり、データ個別あたりのバラツキの程度を求める必要があります。これを分散といいます 。
上の例では、
4)不偏分散()
残差平方和Sを()で割ったもの。
上の例では、
5)標準偏差(または)
不偏分散の正の平方根を標準偏差といい、データのバラツキを知るために最もよく用いられます。
上の例では、
規格値に対するゆとりの計算
分布が余裕をもって規格値を満足しているかどうかは、ヒストグラムによって調べられます。この場合、まず平均値Xが規格値を満足していることを確かめたのち、次に示す方法によって、分布がゆとりをもって規格値を満足しているかどうかを数値計算して、チェックします。
片側に規格値がある場合は、
ここで、は上限規格値、は下限規格値で、上式は上・下限規格値から平均値を引いた絶対値を標準偏差で割ったものが3~4あれば、ゆとりがあるということです。
すなわち、規格値よりプラス・マイナス標準偏差の3~4倍以内に平均値があれば、ゆとりがあることになります。
管理図(シュ ーハート管理図)
管理図の目的
管理図は、ヒストグラムではわからない測定値の時間的変化を加味して、工程が安定しているかどうかを判定し、維持するために用いられます。
すなわち、管理図では、それまでの測定で得られたデータを統計的に処理し、1回の測定に対する平均値()やバラツキの範囲()(最大値と最小値の差)などに対する管理限界線を求め、これを基準にしてその後の測定における平均値やバラツキの範囲を管理することにより、工程の安定性を評価しています。
このため、個々の測定値が規格値を満足しているかどうかを知りたい場合には、規格値と直接対比することができる工程能力図やヒストグラムを用いる必要があります。
管理限界線
管理図は、形の上からいえば品質を表すデータの図式記録の一種ですが、図上に平均値やバラツキの範囲などに対する管理限界線が引かれているところが普通のグラフと違っています。
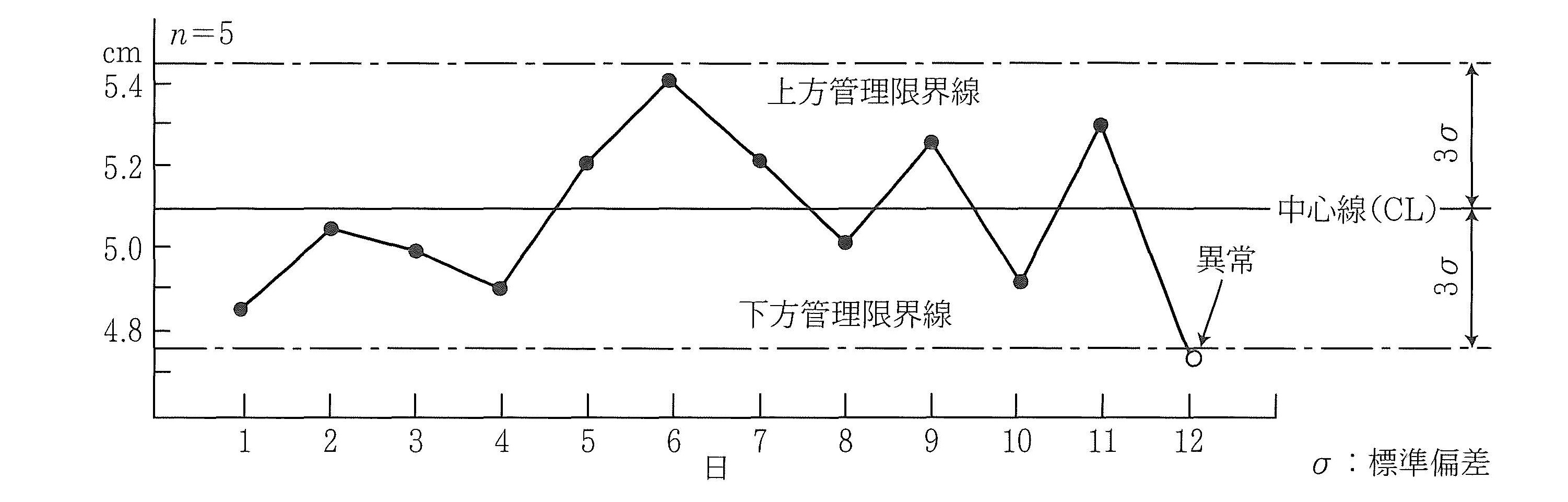
図-10:管理図
この管理限界線は、品質のバラツキが通常起こり得る程度のものなのか(偶然原因による)、あるいはそれ以上の見逃せないバラツキであるか(異常原因による)を判断する基準となるものです。偶然原因によるバラツキは許容し、異常原因によるバラツキを検出して、品質管理に修正が必要かどうかを判断する基準となります。
偶然原因とは、技術的におさえられない原因、またはおさえられることができても、不経済となる原因をいいます。(作業標準通り正しい作業をしていても、品質にバラツキを与える原因)
異常原因とは、技術的に除去できる原因、見逃せない原因をいいます。(作業標準を守らないことや、不備であるためにバラツキを与える原因)
管理図においては、プロットした点(平均値やバラツキの範囲など)が管理限界線の内側に入っており、しかもそれらの並び方にクセがなければ、個々の点のバラツキは偶然原因のみによるものであり、工程は正常で安定した状態にあると判断することになります。
一方、作業標準を守らなかったり、作業標準から外れた作業をすると、点が管理限界線の外側に出たり、中心に集まったり、管理限界線に接近して現れるなどして点の並び方にクセが出る。このため、異常原因の存在が推測され、工程は異常で安定した状態にないと判断することになります。
管理図の種類
建設工事で取り扱っているデータには、連続的な値と離散的な値とがあり、連続する値を計量値、離散的な値を計数値といいます。
連続的な値である計量値とは、例えば舗装の厚さや強度、重量などのように量的に測定できる値をいいます。これに対して、離散的な値である計数値とは、鉄筋100本中不良品が5本あるとか、1か月の事故が1回、2回というように測定されるもので、5.5本とか1.8回とかの値を取り得ないものをいいます。
品質管理に管理図を用いる場合は、取り扱う対象が計量値であるか計数値であるかによって、使用する管理図が異なります。主な管理図の種類として、次のようなものがあります。
- 計量値の管理図(連続的な値)
- -管理図(群の平均値とバラツキの範囲を用いて群間の違いや工程の分散を評価する)
- -–管理図(個々の測定値とバラツキの範囲を用いて工程を評価する)
- 文管理図(メディアンを用いて群間の違いを評価する)
- 計数値の管理図(離散的な値)
- 管理図(不適合品率を用いて工程を評価する)
- 管理図(不適合品数を用いて工程を評価する)
- 管理図(サンプルに生起した不適合数を用いて工程を評価する)
- 管理図(サンプルの単位あたりに生起した不適合数を用いて工程を評価する)
これらの管理図のうち、建設事業の場で比較的多く用いられているのは、-管理図ならびに-–管理図であり、管理図を理解するにはこの2つを理解すればよいと考えられます。
X-R管理図
X-R管理図の概要
-管理図は、最も代表的な管理図であり、重さ・長さ・時間などの計量値の管理に用いられています。
群分けしたデータの平均値Xとそのバラツキの範囲Rの変化を管理する、管理図と管理図とからなります。この2つの管理図を対にして、各群の試料における平均値とバラツキの範囲の変化を同時にみることで、工程の安定状況をとらえることができます。
管理図は、群の大きさn(一度に計測するデータの数を群の大きさで表し、計測する回数を群の数で表す)がより多くなると性能が悪くなるので、一般に、が以下の場合に用います。
X-R管理図の作り方
手順1. 予備データの準備
1群(1組)に含ませるデータの数(群の大きさ)は、通常3~5個がよいです。比較的最近の群を集め、予備データとします。この予備データは、今後管理する諸データの代表となるようなものでなければなりません。
具体的には、時間を追って生産している場合は日・週ごとなど、道路・河川工事の場合は起点からの距離・測点ごとなど、その特性が大体似ている範囲を群とします。
手順2. 平均値の計算
群の平均値を計算します。一般に、平均値の桁数はデータの桁数より1桁下まで求めます。(2桁下を四捨五入)。
手順3. バラツキの範囲Rの計算
群ごとに最大値と最小値の差を計算します。
手順4. 総平均の計算
群ごとの平均値の合計を、さらに群数(組数)で割って全体の総平均を計算します。のさらに1桁下まで求めます。
手順5. バラツキの範囲の平均Rの計算
群ごとのの合計を、さらに群数(組数)で割ってを計算します。
手順6. 管理線の計算
- 管理図
- 中心線
- 上方管理限界線
- 下方管理限界線
- 管理図
- 中心線
- 上方管理限界線
- 下方管理限界線
、は群試料の大きさ、すなわちデータ数によって決まる定数で、下表から求める。 ただし、はの場合、「LCLは存在しない」と決められているため、考えない。
2 | 1.88 | 考えない | 3.27 | 2.66 |
3 | 1.02 | 考えない | 2.58 | 1.77 |
4 | 0.73 | 考えない | 2.28 | 1.46 |
5 | 0.58 | 考えない | 2.12 | 1.29 |
6 | 0.48 | 考えない | 2.00 | 1.18 |
7 | 0.42 | 0.08 | 1.92 | 1.11 |
8 | 0.37 | 0.14 | 1.86 | 1.05 |
9 | 0.34 | 0.18 | 1.82 | 1.01 |
手順7. 管理図の記入
- 管理図を上部に、管理図を下部に配置し、群番号をそろえて対照できるようにします。
- 品質特性、測定単位、工事名、管理図番号などの必要関係事項を記入します。
- 管理図、管理図の左側に、それぞれ、を記入します。
- 管理図の左上に試料の大きさを記入します。
- 管理線の記入の仕方は、次のようにするとはっきりします。
- 予備のデータのとき、中心線は実線、管理限界線は破線、予備データの最後の組番号まで引きます。管理線の延長は、予備データによる管理線と区別するため、中心線は実線で描きますが、管理限界線は一点鎖線で描きます。
- 点の記入は、はっきり大きめにします。
- 普通は、は直径1mmぐらいの「・」、Rは各線の長さが2mmぐらいの「×」印で打点します。管理限界から出た点は、「○」など赤丸をつけて、はっきりするようにしますとよく、限界線上の点は管理外れとします。打点した点は、群番号順に細い実線で結びます。
- 予備データの最後の組のあとに締切り線を引いて、どこまでが予備データであるかを明確にします。
手順8. 安定状態の判定
打点した、がそれぞれ管理限界線内でクセがなければ、安定状態であると判定します。もし管理限界線外に打点されれば、その点について原因を調査し、原因を除去し再発を防ぎます。安定状態であれば、手順10.に移ります。
手順9. 管理線の再計算
手順8.で処置できたら、その点を除いて管理線の再計算を行い、管理線の中心線、管理限界線を引き直します。
管理限界線外に打点された点でも原因がわからないか、またわかっても処置できなければ、その点は除かないで再計算に用います。
はじめに管理限界線内にあった点は、再計算したために、新しい管理限界線から飛び出してもそのまま用います。
手順10. 規格値との比較検討
以上の手順を踏んで、管理線の計算に用いた個々のデータ全部を使ってヒストグラムを作り、規格値と比較検討をします。
手順11. 管理限界線の決定
品質特性値が十分なゆとりをもって規格を満足し、しかも安定状態にあることがわかったら管理限界線を延長して、工程に対して当分の間の管理限界線とし、この状態を維持するように管理します。
以上の手順で-管理図が作れますが、建設現場のように予備データを多数とることが困難な場合は、本工事のデータを用いて、次のような方式で管理します。
最初の5群で次の5群を管理し、それまでの10群のデータで次の10群を管理し、それまでの20群のデータで次の20群を管理し、その後は最近の20群のデータにより次の20群を管理します。このような方式は、20~30群のデータをとるまでに工事が終わってしまうような場でも適用できます。これを、5-5-10-20-20方式といいます。
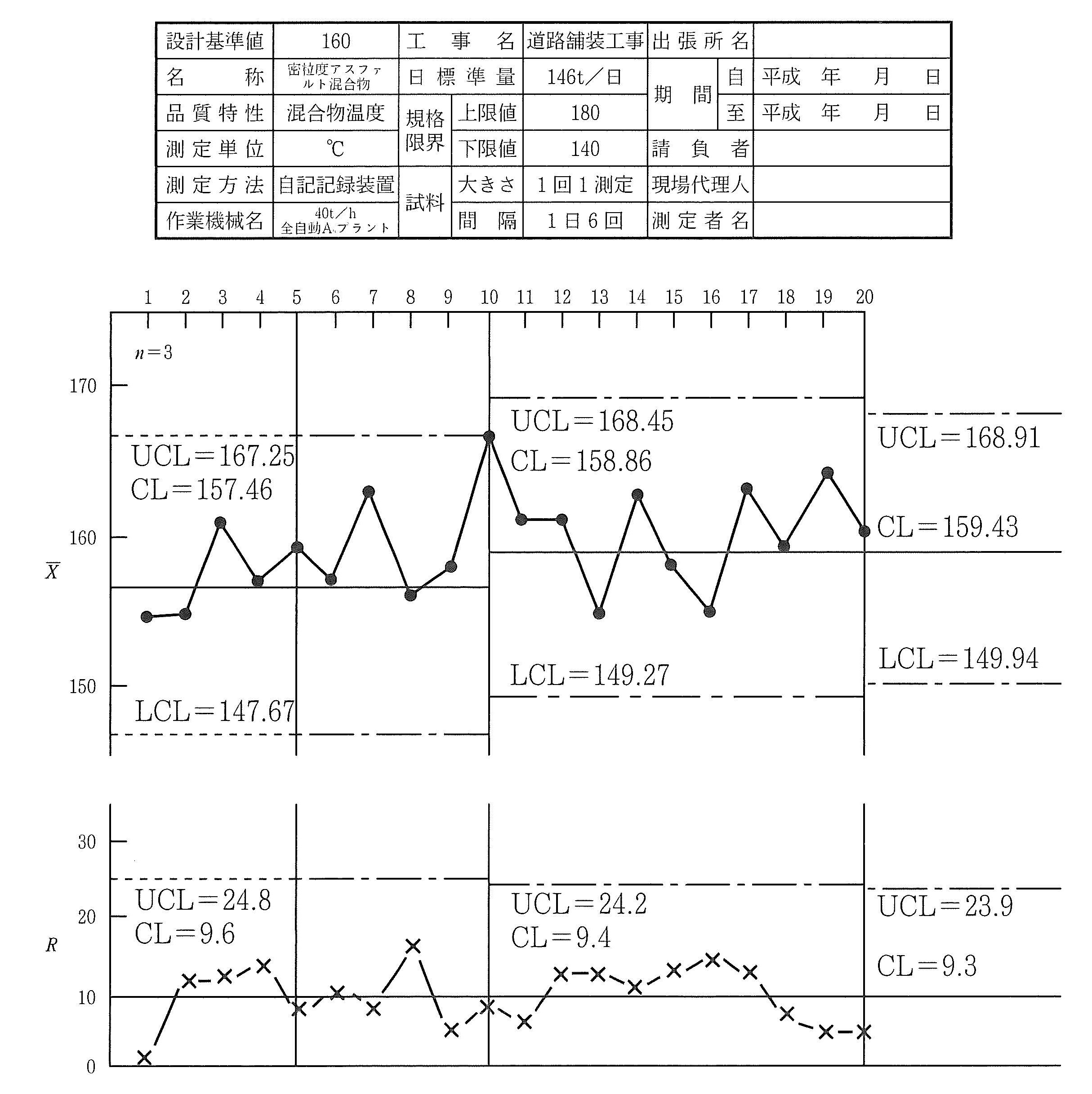
図-11:X-R管理図の例
品質検査の方式と品質管理の例
母集団とサンプリング
ある製品の品質を管理しようとするとき、その製品が数多くある場合、または数えられるほどであるが種類が多い場合、その全部を調べて品質を管理することは不可能ではありません。また、仮に可能であっても非常に不経済です。
そこで一般には、調べようとする対象の集団からその一部を取り出して、その一部のデータによって集団の性質を統計的手法により推測する方法がとられています。この場合の調べようとする集団のことを母集団といいます。
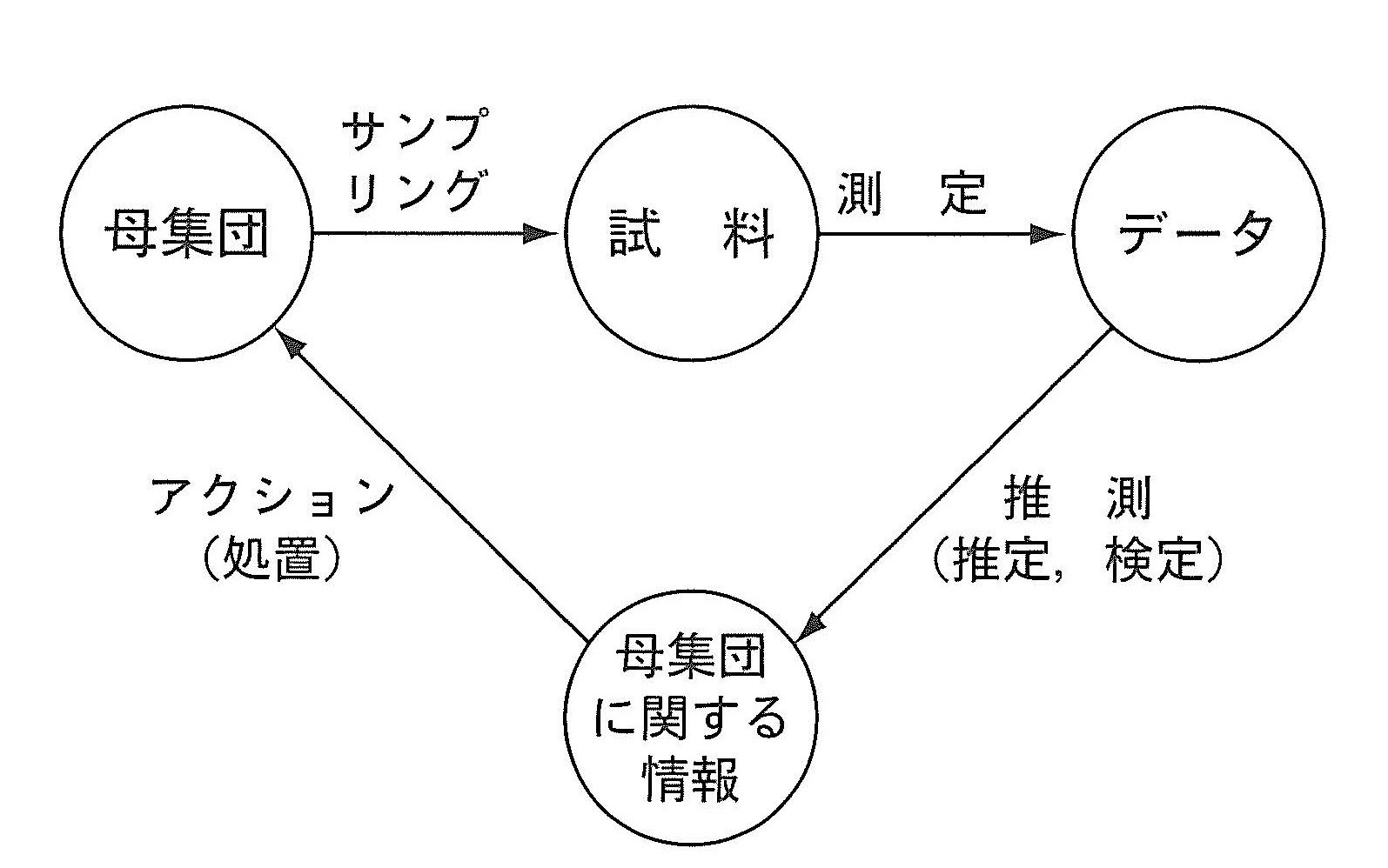
図-12:母集団とサンプリング
母集団からその一部を取り出したものをサンプル(試料)といい、サンプルを得る方法をサンプリング(試料抽出)といいます。また、母集団を構成する単位体を、検査などのために、ひとまとまりにしたグループをロットといいます。抜取検査は、このロットからサンプルを抜き取って検査し、サンプルの中の不適合の数などを基にして、各ロットの合否を判定します。これらのサンプルから得られた品質特性に関する測定値をデータ(データ値)といいます。
サンプリングに基づいてその母集団の姿を正しく把握し処置を行うためには、母集団を正しく代表するようなサンプリングをすることが重要であり、JISでは乱数表を用いるなど無作為抽出(ランダムにサンプリング)する方法を定めています。
全数検査と抜取検査
全数検査
品物1個1個を全部検査する(100%検査)もので、良品と不良品を選別する目的で行われ、次のような場合に適用されます。
- わずかの不良品混入も許せない場合
- 検査が容易に行える場合
- ロットの品質をよくしたい場合
- ロットの大きさが小さくて、抜取検査の意味がない場合
抜取検査
全数検査をすることが現実には不可能かあるいは著しく不経済な場合、検査の対象を一定の数量から成るロットに分割し、各ロットからその中の一部を試料として抜き取って試験します。その結果をロットに対する判定基準と比較して、そのロットの合格不合格を判定する検査方法です。
例えば、舗装工事の出来形検査においては、1ロットの大きさは、同一の設計と施工による各工種(例:路盤、路床、アスファルト層など)に対して、舗装面積で10、000m2以下とされています。
抜取検査は、次のような場合に適用されます。
- 破壊検査の場合
- 連続体の場合
- 検査個数の多い場合
- 検査項目の多い場合
- 有効な品質情報を得たい場合
- 管理者が、構造物の実体に精通したい場合
抜取検査には、次の種類があります。
- 1回抜取検査: ロットからサンプルをただ1回抜き取り、その試験結果で合否を判定する方法。
- 2回抜取検査: 1回目で合格、不合格の判定ができないロットに対し、2回目の抜取検査を行い、1回目の結果 との累計成績によって合否を判定する方法。
- 多数回抜取検査: 2回抜取検査をさらに広げ、ある一定回数まで検査を行って判定する形式。
- 逐次抜取検査: 1個ずつ、または一定個数ずつ試験しながら、その集計成績をその都度判定基準と比較して判定する形式。
これらは、それぞれ目的によって組み合わせて用いられていますが、一般に、建設工事の場合は、1回抜取検査により行われています。