工程管理
工程管理の概説
工程管理の目的
工事の施工にあたっては、所定の図書、仕様書に基づき、定められた工期内に、所定の品質(出来形を含む)の目的構造物を経済的に竣工させることが必要となります。工程管理は、これを効果的に実施するための手法であり、施工計画をもとに、現場状況の変化に適切に対処して、工程全体の進度を管理することを目的としています。
工事における三大管理項目についてみると、工期は着工から竣工までの各工程の時間的な系列を所定の範囲に収めることによって守られ、品質は各工程における確かな施工で確保され、工事の原価は各工程で発生する費用を管理することによって予定原価内に収めることができます。このように、三大管理項目の目標を実現することは、工程そのものと密接不可分であり、工程管理が工事を総合的に管理するうえで重要な意味を持っていることがわかります。
工程管理は、基本的には、工事の着工から完成までの施工計画を時間的に管理することです。工程管理にあたっては、現場の状 況変化に応じて、施工計画をあらゆる角度から評価・検討し、機械設備、労働力、資材、資金などを最も効果的に活用するようにしなければなりません。従来、ともすると工程管理は工期を守るための進度管理だけが目的と理解されていましたが、先述のように、原価管理や品質管理をはじめその他の管理にも大きく影響するものであり、総合的な視点からその重要性を理解する必要があります。
工程管理の手順と内容
工程管理の手順は、計画(P)→実施(D)→検討(C)→処置(A)の順となります。各段階における一般的な実施項目は、次のとおりです。
- Plan 計画を立てる。
- 施工計画(施工順序、施工法などの基本方針の決定)
- 工程計画(作業手順と日程の計画、工程表の作成など)
- 使用計画(労務、機械設備、資材、資金などの所要時期、品目、数量および輸送などの計画)
- Do 計画に基づいて実施する。
- 工事の指示、承諾、協議、段階検査
- Check 計画と実施結果を比較検討する。
- 作業量管理(作業量、資材使用量などの実績の整理とチェック)
- 進度管理(工程進捗の計画と実施の比較、進捗報告など)
- 手配管理(機械、労力、材料などの手配)
- Action 当初計画とずれていれば是正処置をとり、また必要に応じて当初計画を見直す。
- 是正処置(作業改善、工程促進、再計画など)
なお、工程管理は、施工計画の立案と計画を実施する統制機能(P.D)と、施工途中で計画と実績を評価し、改善点があれば処置を行う改善機能(C.A)に大別できます。
工程管理の基本
工程管理の基本は、施工管理全般と整合した適正な施工速度を設定し、保持することです。
工程管理の実施にあたっては、次のことに十分留意しなければなりません。
- 工程計画は、所定の品質の構造物が、経済的に、所定の工期内で施工できるように作成する(施工管理の3本柱の満足)。
- 工程計画では、品質の確保と経済的施工の両立が実行可能となる最適工期を選定する。
- 工程計画は、工程の進捗にあわせた施工管理が可能な内容とする。
- 工程管理においては、実施工程を評価・分析し、その結果を踏まえて計画工程を修正する。
施工速度
施工速度(工程という場合もある)の設定は、工程管理における基本となるものです。施工速度と経済性との関係などについて、以下に概要を説明します。
1 工程と単位原価
一つの工事(一部分または全体)に 関する工程(施工速度)と原価の関係は、一般的に、図-1に示すようなものとなります。施工速度が遅いと施工効率が悪く単位あたりの原価は高いが、施工速度を速めると出来高が増加して単位原価は低減します。さらに、ある限度を超えて施工速度を速めようとすると、機械の大型化や高価な資材の使用が必要となり、単位原価は上昇します。単位原価の上昇が著しい例は、突貫工事です。
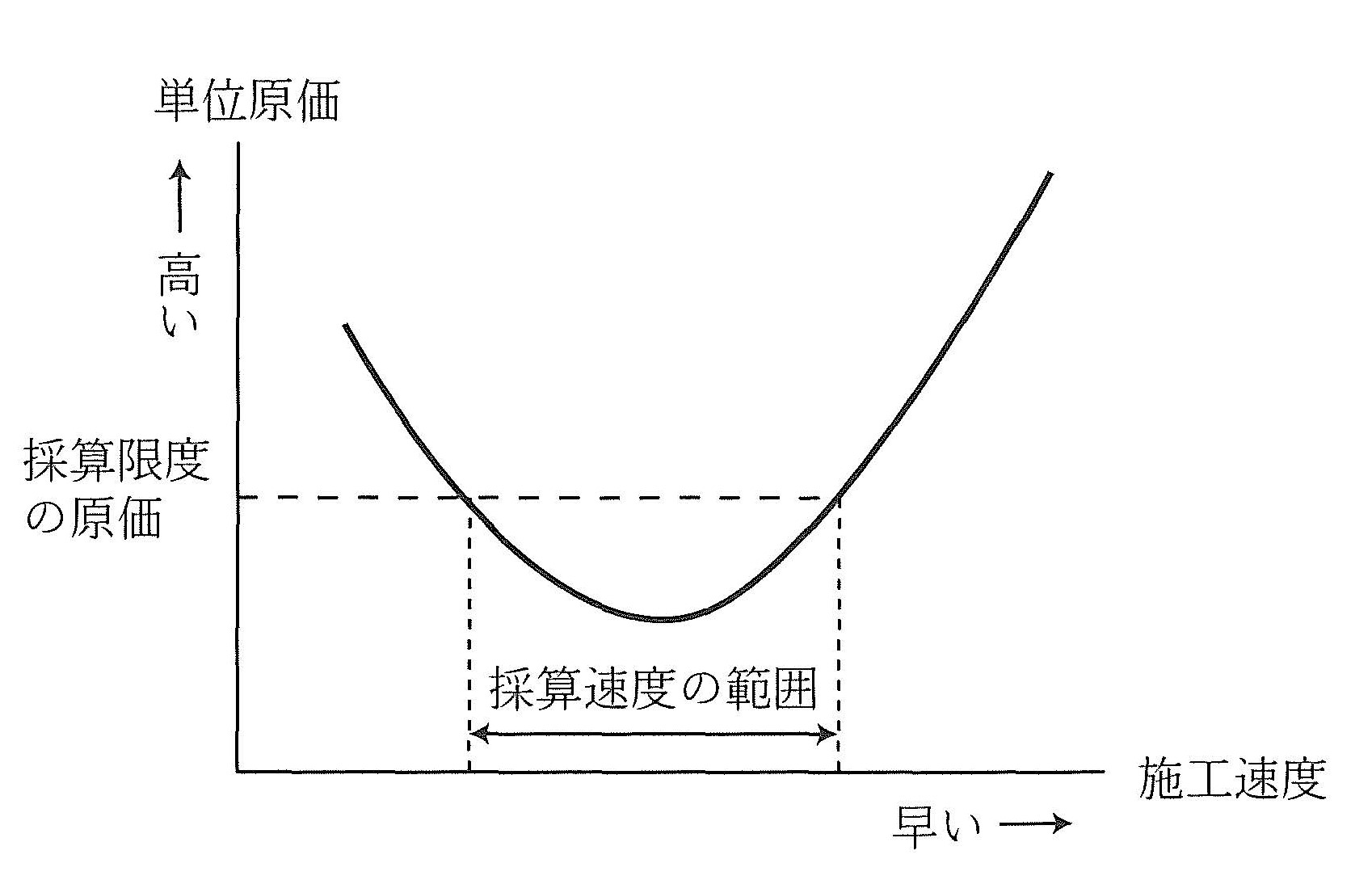
図-1:工程と原価
実行予算の立案にあたって、単位原価には採算を確保するための採算限度となる原価があり、単位原価が採算限度の原価以下となる工程が採算速度です。また、工事工程は、施工速度が採算限度の範囲内で工期を満足し、最も効率的かつ経済的となるよう設定する必要があります。
2 施工出来高と工事総原価
一定の施工速度のもとにおける施工出来高(施工量)と工事総原価との関係は、一般に、図-2に示すようなものとなります。工事総原価は、施工出来高に関係なく必要な一定の固定原価と、施工出来高の増加に応じて増大する変動原価とから成ります。
- 固定原価:現場事務所費用、建設機械の損料、職員給与他現場諸経費など、施工量の増減に関係ない原価
- 変動原価:材料費、労務費、機械運転経費など、施工量に比例する原価
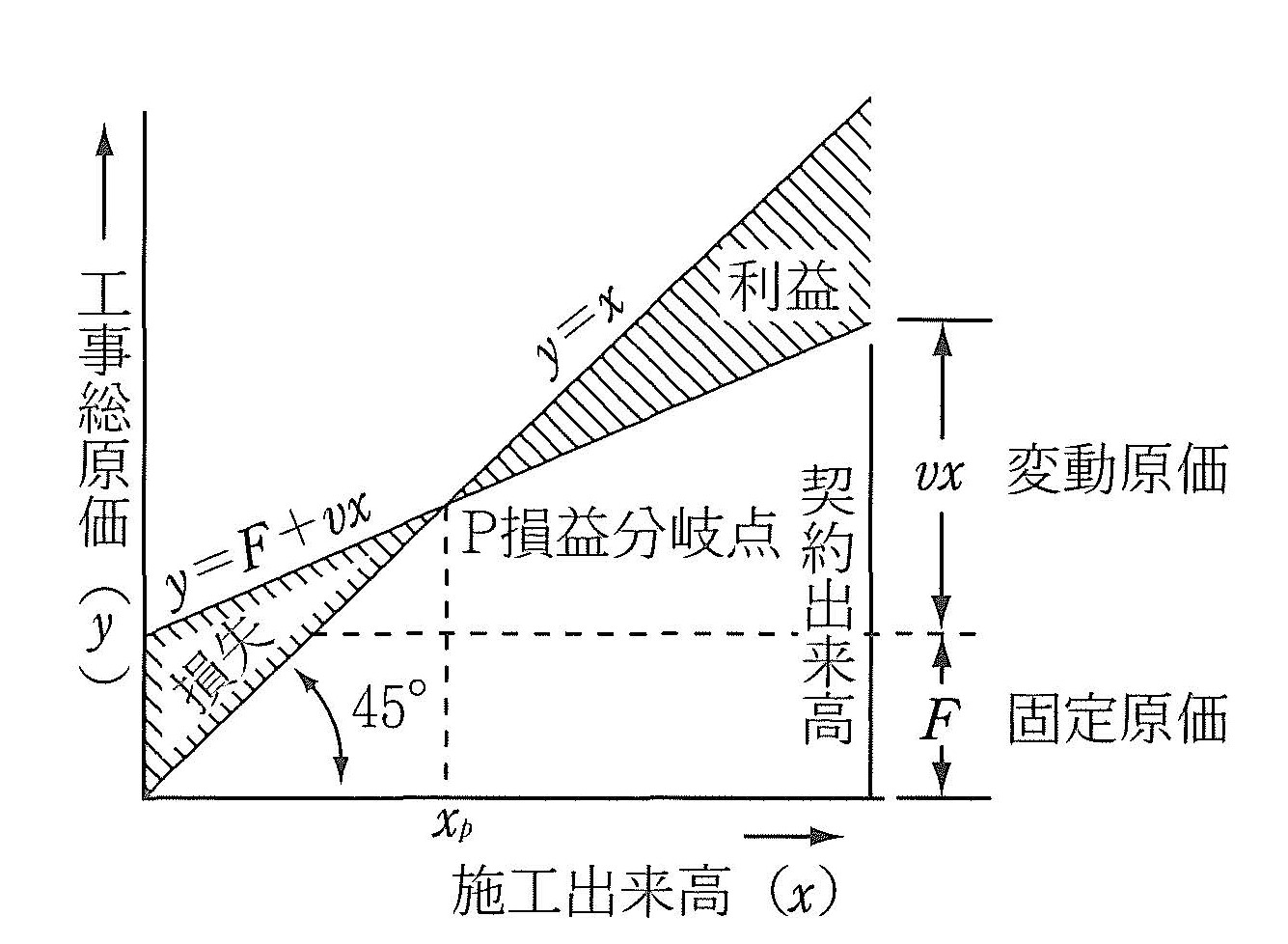
図-2:利益図
工事総原価 (原価曲線)= 固定原価 + 変動原価
一般に、変動比率は施工条件で変化するので、工事総原価は直線とはなりませんが 、変動原価の上昇を抑えるために、なるべく直線を維持するように工程を計画し管理することが望ましいです。そのためには、次に示す、外部および内部の2条件が維持される必要があります。
- 外部条件
- 設計、仕様、数量、工期、契約原価など発注者の要求に変化のないこと。
- 地質、天候など自然条件に予想外の変化のないこと。
- 物価、労賃など一般市況に大きな変化のないこと。
- 内部条件
- 工事用仮設備、機械、管理組織などの規模や施工法に大きな変化のないこと。
- 施工量に比例的でないような賃金方式を採用しないこと。
- 材料の消費量が施工量に比例的であること。
- 材料購入単価、支払賃金率に変化のないこと。
- 施工される工種の構成比率に大きな変更のないこと。
これらの条件が適切に維持・管理され、図-2のような原価曲線の関係が成立する場合、工事は「経済速度で施工されている」といい、目標とする施工出来高が大きいほど利益が上がる健全経営となります。また、予期し得ない理由により、上記(2)内部条件が維持されず、不利な方向に大きく変動した場合は、損益分岐点が著しく右方向にずれて、契約施工出来高を達成しても利益が上がらず、損益分岐点が現れない赤字工事となります。その極端な例が、突貫工事です。
3 採算速度
図-2より、契約施工出来高が損益分岐点の施工出来高と等しい場合には、工事は採算を確保するための最低採算速度の状態にあります。工事運営上、工程計画と工程管理においては、常にこれ以上の施工速度を保持できるようにしなければなりません。
- 損益分岐点:工事運営に要する収入と支出が等しくなり、黒字にも赤字にもならない状態
- 採算速度:損益分岐点の施工出来高以上の施工出来高をあげるときの工程速度
経済的な工程計画の立案
工事を運営するためには、突貫工事とならないように、経済速度で最大限に施工量の増大を図る工程計画を立案する必要があります。そのために、固定費を最小限にし、変動費率を極力小さくすることが重要であり、次の事項に留意する必要があります。
- 仮設備工事、現場諸経費を必要最小限にすること。
- 施工用機械設備、仮設資材、工具などは必要最小限とし、できるだけ反復使用すること。
- 作業員は、合理的最小限の一定数とし、全工事期間を通じて稼働作業員数の不均衡をできるだけ少なくすること。
- 施工の段取り待ち、材料待ち、その他機械設備の損失時間をできるだけなくすこと。
最適工期の決定
最適工期とは、建設費のうち、直接工事費と間接工事費の合計金額が最も経済的となる工期です。
1 直接工事費と間接工事費
直接工事費と間接工事費の内容および性質は、次のとおりです。
- 直接工事費
- 労務費、材料費、仮設備費、機械運転費など
- 一般に、作業速度を経済速度以上に速めると、超過勤務、多交代作業、多人数同時作業等の非能率作業の発生、高価な材料、高価な機械や工法の採用などによって、直接費は増加する。つまり、工期の短縮に伴って、直接費は増加することになる。
- 間接工事費
- 共通仮設費、現場管理費、減価償却費、金利など
- 一般に、工期の延長にしたがって、ほぼ直線的に増加する傾向にある。
2 最適工期の選定方法
最適工期は、直接工事費と間接工事費の組合せが最小となるような工期として求めることができ、工事費曲線(図-3)で表されます。
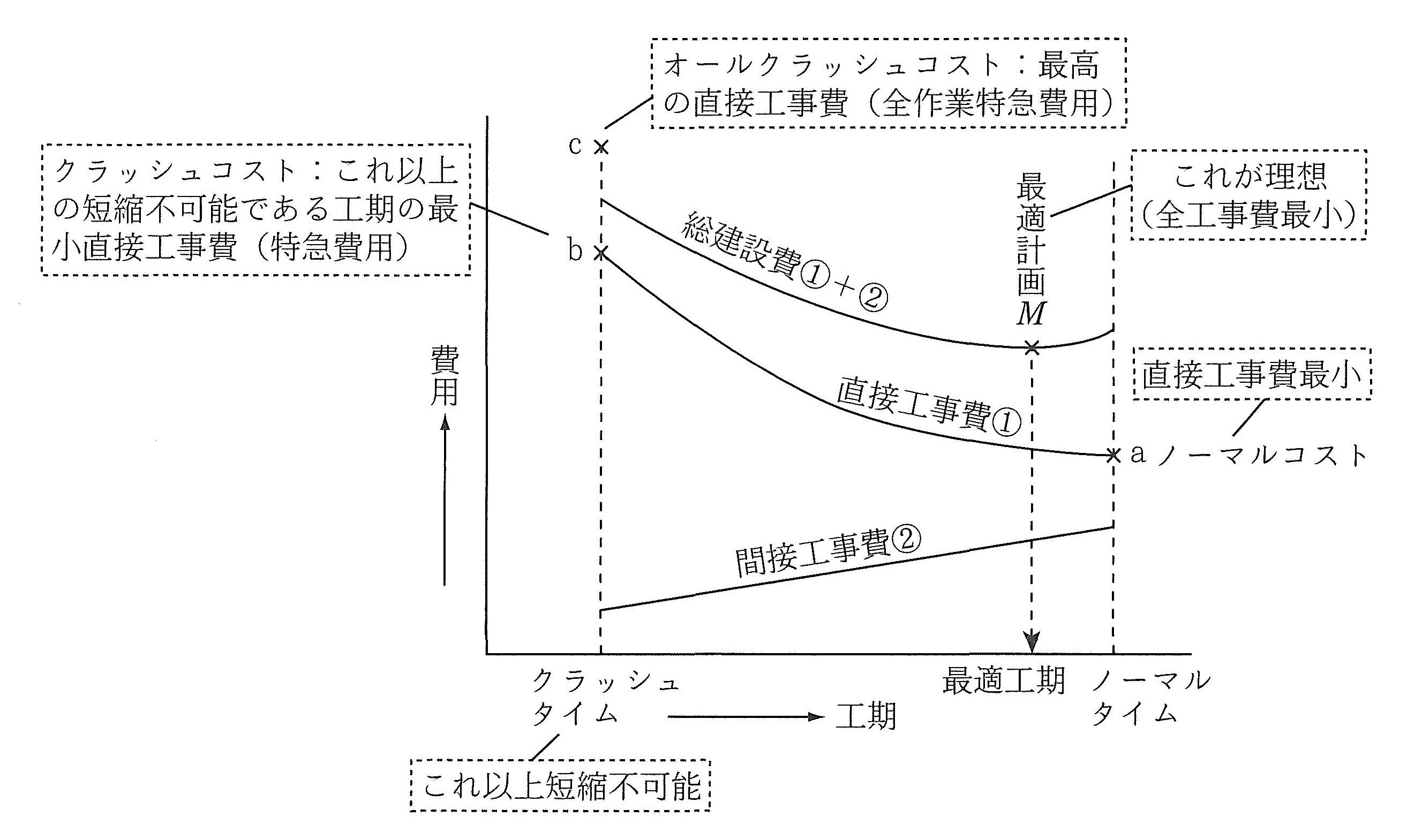
図-3:工事費曲線
- 直接工事費と工期
- 工事の直接工事費が最小となる最長工期、すなわちノーマルタイムより工期を短縮した場合の最小直接工事費の算出方法にCPM(クリティカルパスメソッド)と呼ばれ るものがあり、図-3の曲線abとして得られます。
- 間接工事費と工期
- 間接工事費は、工期の短縮にしたがって減少します。通常、ノーマルタイムで最大であり、クラッシュタイムで最小を示し、その間をほぼ直線的に変化します。
- 総建設費と最適工期
- 図-3から得られる総建設費曲線が最小となる点Mを求め、それに対応する工期が最適工期となります。
実際の工事では、工期を短縮することで資源(人や機械)を次工事へ投入でき、得られるメリットも大きいです。こうした外部条件も勘案して工期を検討することが必要です。ただし、工期を短縮し過ぎると品質低下や安全上の問題が発生し、これらを補足するためのコスト増が予想されます。したがって、総合的な観点で適正な工期を検討することが重要です。
工程計画の作成手順
工程計画は、工事の種別、内容、工期および現場状況などの施工条件が明らかになると、それに応じて施工方法その他全体の施工計画の大綱が自然に決定されます。その過程を工程計画立案の手順として示すと、次のようになります。
- 工種分類に基づき、基本管理項目である工事項目(部分工事)について、施工手順を決める。
- 各工種別工事項目の適切な施工期聞を決める。
- 全工事が工期内に完了するように、前述の工種別工程の相互調整を行う。
- 全工期を通じて、労務、資材、機械の必要数を均し、過度の集中や待ち時聞が発生しないように工程を調整する。
- 以上の結果をもとに、全体の工程表を作成する。
このような手順に従って適切な工程計画を作成するためには、建設機械の選定、作業員、材料の供給予測のほか、現場条件や気象などの自然条件など、あらゆる関連条件を考慮して計画することが必要です。
工程図表
工程図表の種類
1 工程図表による管理
工程管理では、各種の工程図表を作成し、実施と検討のための基準として使用します。その際に、工程図表を基本工程表(全体工程表)と部分工程表および細部工程表とに分けて扱うことがあります。基本工程表は、工事の主要な工種ごとに区分して施工順序を組み合わせ、全体的に工期を満足させるように作成したものです。部分工程表および細部工程表は、基本工程表にのっとり、各工程をさらに詳細に組み立てたものであり、時間単位も月から日へと細かくなっています。
工程図表は、前述の「経済的な工程計画の立案」で述べた趣旨にのっとり、作業可能日数の算定、平均施工速度によ る1日標準施工量の算定、部分工事に必要な日数の算定、施工順序の決定、最適工期の決定などを行って確定した工程を図表化したもので、工事の施工とその管理を行うために作成するものです。
工程図表には、横線式工程表(バーチャート、ガントチャート)、斜線式工程表(座標式工程表)、曲線式工程表(グラフ式工程表、出来高累計曲線)、工程管理曲線(バナナ曲線)、ネットワーク式工程表があります。
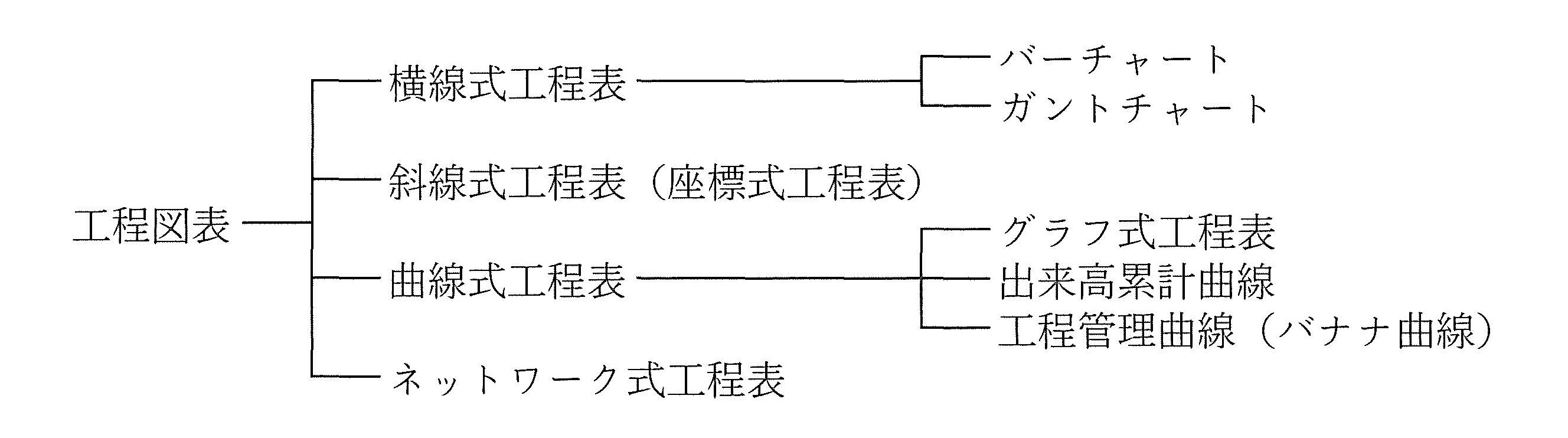
図-4:工程図表の分類
2 横線式工程表
バーチャート
バーチャートの長所は、作成および修正が容易で、各作業の所要日数や進捗状況が直観的にわかることです。一方、短所は工期に影響する作業が不明確である点です。バーチャートを作成する手順は、次のとおりです。
- 全体を構成するすべての部分作業(部分工事)を縦に列記します。
- 利用できる工期を横軸に示します。
- すべての部分工事の施工に要する時間をそれぞれ計画します。
- 工期内に全体工事を完成できるように、3により計画した各部分の所要時間を図表の上にあてはめて日程を組みます。
このうち、日程の組み方には、次の3通りの方法があります。
- 順行法は、施工順序にしたがって、着手日から決めていく方法です。
- 逆算法は、逆に竣工期日からたどって、着手日を決める方法です。
- 重点法は、季節や工事現場条件、契約条件などに基づいて、重点的に着手日、終了日をとりあげ、これを全工期の中のある時点に固定し、その前後を順行法または逆算法で固めていく方法です。
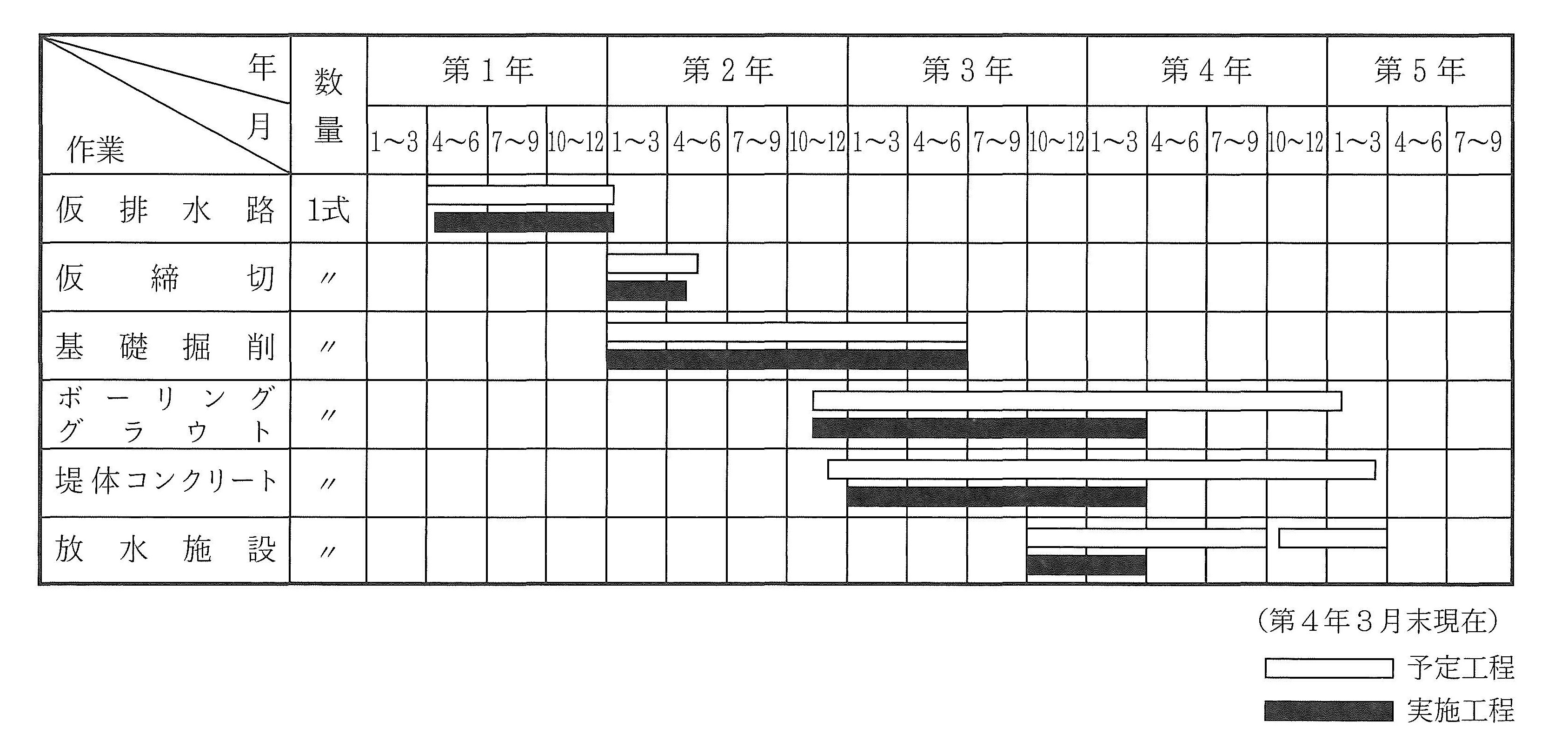
図-5:バーチャートの例
ガントチャート
ガン卜チャートは、各作業の完了時点を100%として横軸に達成度をとり,縦軸にはパ-チャートと同様、部分作業(部分工事)を列記する。ガントチャートの長所は、作成が容易で、各作業の現時点での進捗度合がよくわかることである。一方、短所は、作業に必要な日数がわからず、工期に影響する作業が不明確なことである。
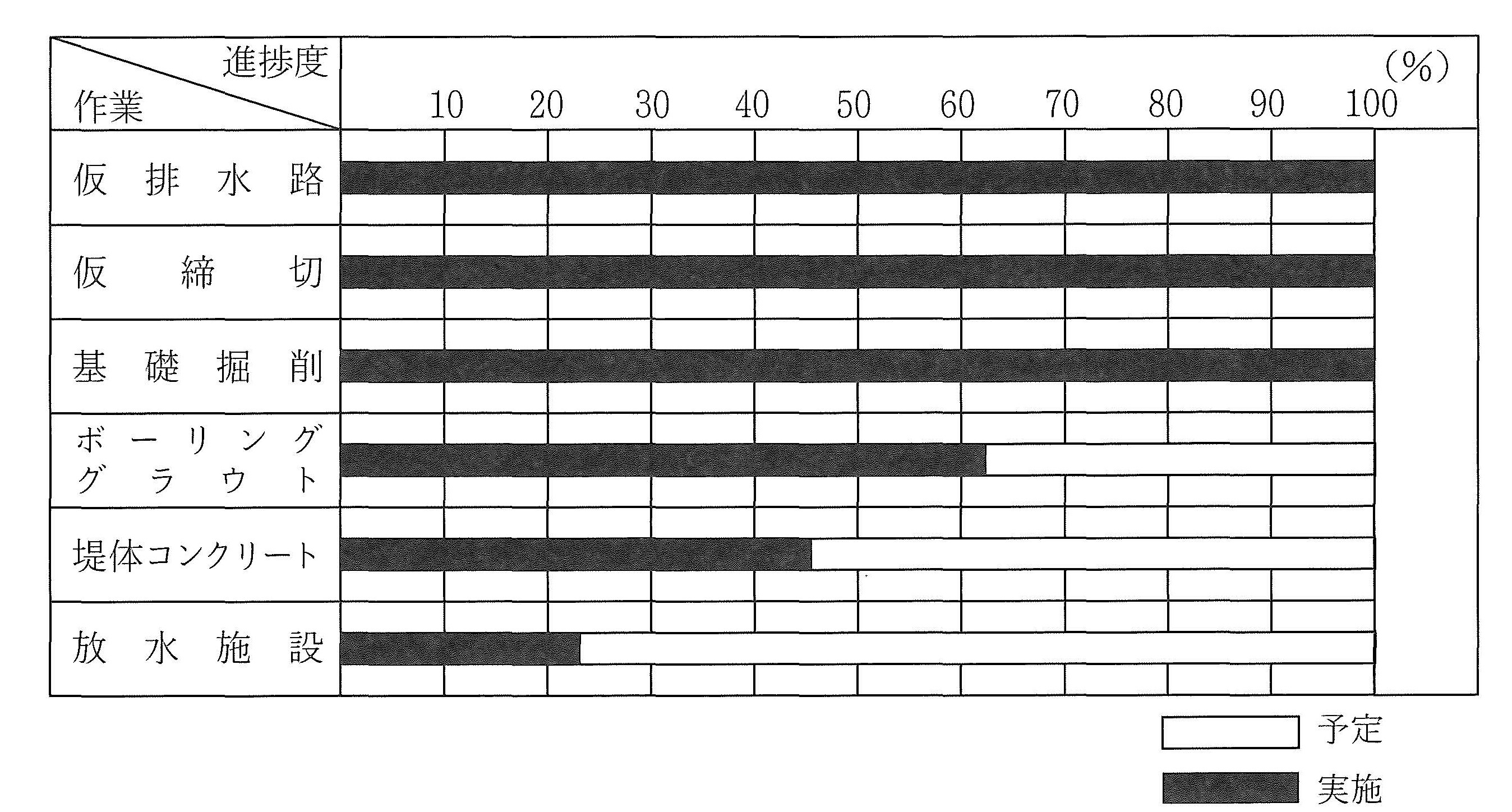
図-6:バーチャートの例
3 斜線式工程表
斜線式工程表(座標式工程表)は、横軸に区間(距離程)をとり、縦軸に日数(工期)をとって表すものです。
斜線式工程表の長所は、ト ンネル工事のように進捗が距離のみによる場合は、すべての工種が枠内に表現でき、また、施工場所と施工時期の進捗状況が直視的にわかることです。一方、短所は、工種間の相互関係が不明確で、部分的な変更があった場合に全体に及ぼす影響がわかりにくいことです。
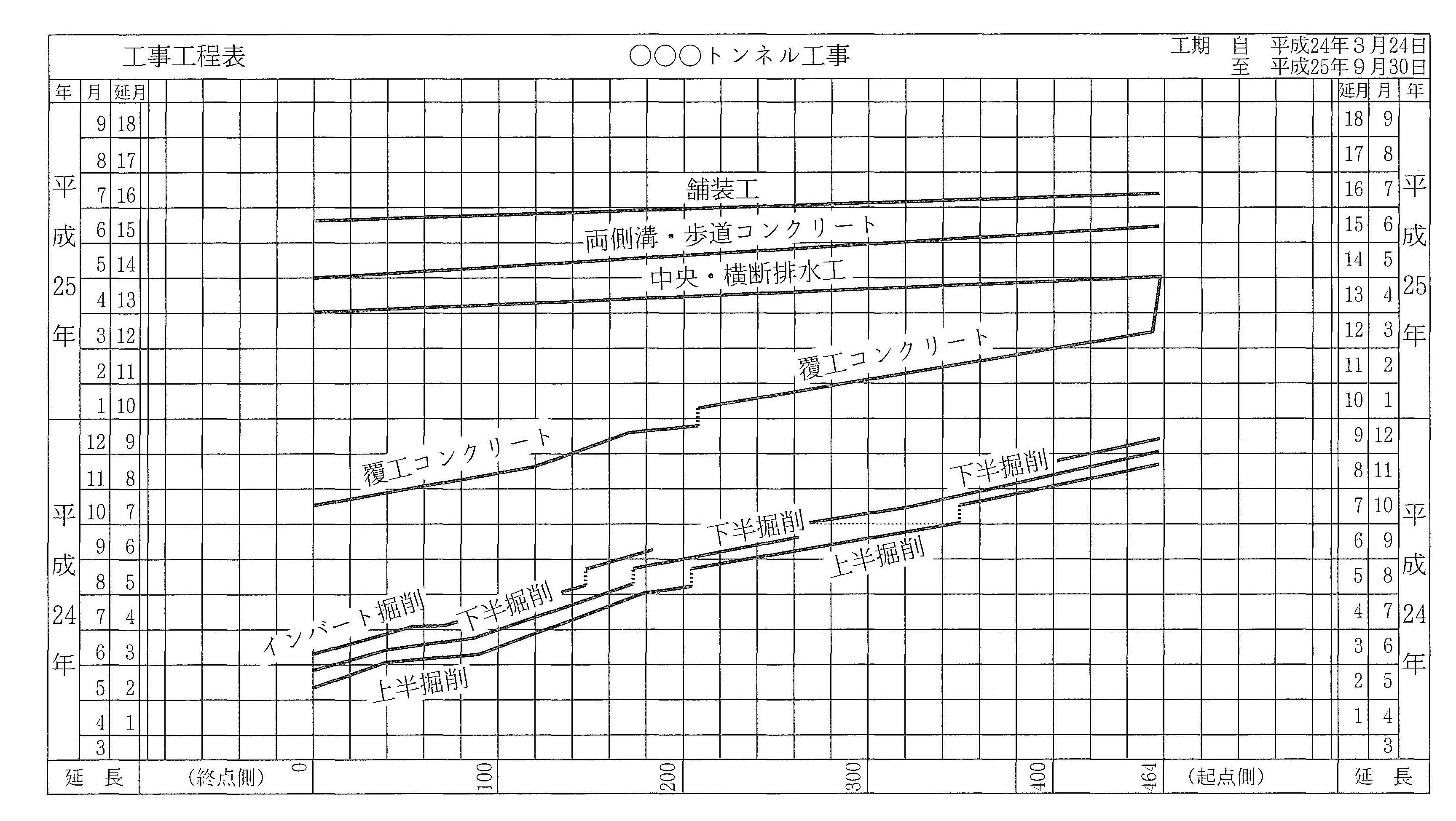
図-7:斜線式工程表の例
4 曲線式工程表
グラフ式工程表
工事や作業の開始に先立って曲線式工程表を作り、作業の進みぐあいに伴ってこれに実施出来高の曲線を入れ、両方の曲線を比較対照して工程を管理することは、予定の工期に工事を完成するために必要です。また、計画工程に沿って作業を進めることが機械、労力、資材などの損失を防ぐことにつながり、経済的に工事を進めることができます。
グラフ式工程表は、横軸に工期をとり、縦軸に各作業の出来高比率(%)をとって、工種ごとの工程を斜線で表した図表です。グラフ式工程表の長所は、予定と実績との差を直観的に比較しやすいこと、また、どの作業が未着工か、施工中か、完了したかの進推状況が一目瞭然なことです。一方、短所は、各作業の相互関連と重要作業が不明確なことです。
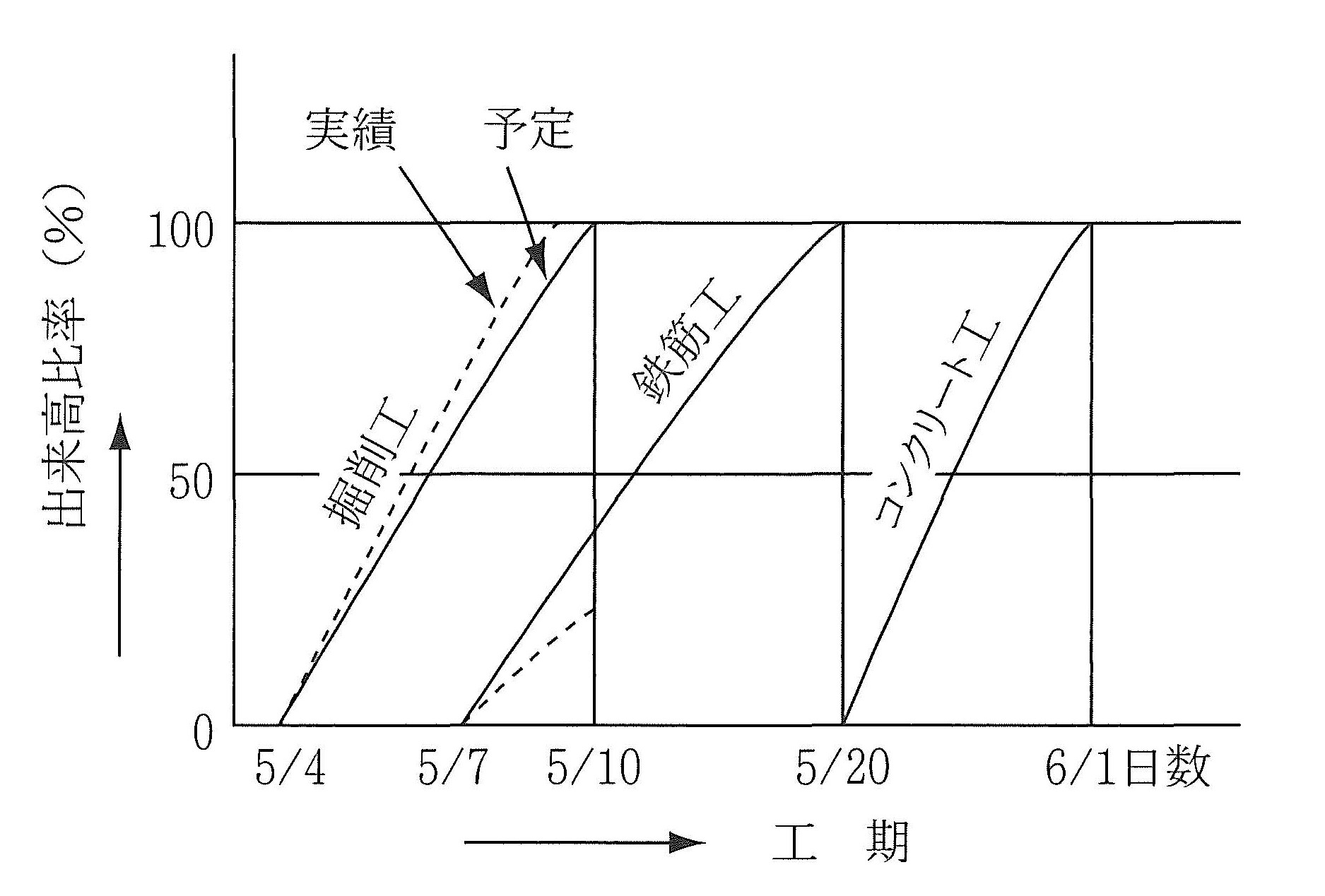
図-8:グラフ式工程表の例
出来高累計曲線
出来高累計曲線は、横軸に工期をとり、縦軸に出来高累計をとって、全体工事に対する月ごとの出来高比率を累計した曲線です。
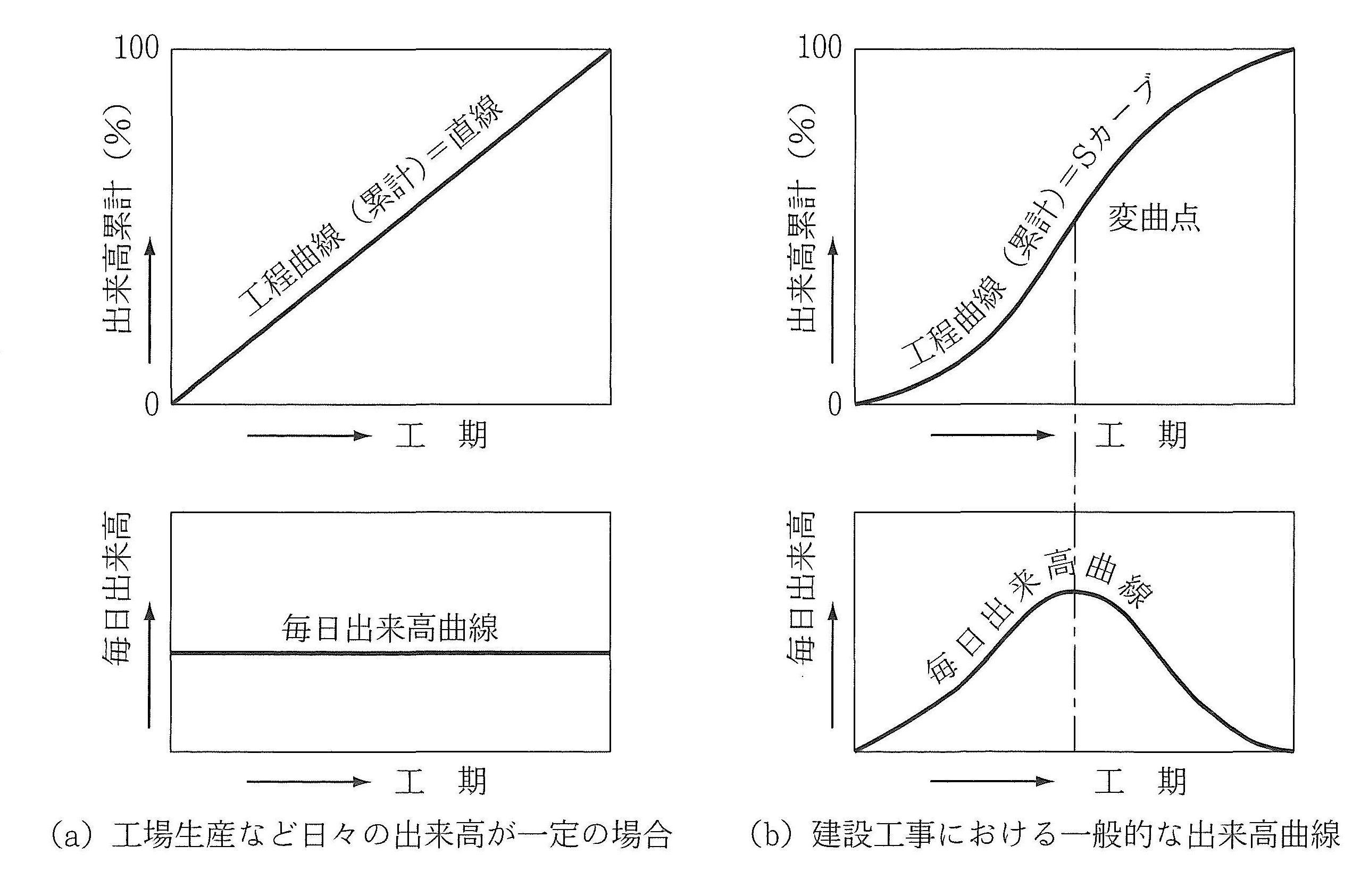
図-9:工程曲線と毎日出来高曲線
一般に、工期の初期には仮設や段取りがあり、また終期には仕上げや後片付けなどがあるため、工程速度(1日の出来高)が初期(最盛期)より低下するのが普通です。
つまり、毎日の出来高は工事の初期から中期に向かって増加し、中期から終期に向かって減少していきます。このとき、出来高累計曲線は変曲点を持ったS型の曲線となります。この曲線をS字カーブと呼んでいます。工期の後半になると上方に凸形となり、一般にS型となりますが、ときには実施工程曲線が終期に来ても上方が凹形となることもあります。
このような型の工程曲線は、工程遅延を取り戻すために、最後のほうで突貫工事を続けたことを表しており、避けなければなりません。このためにも、工事初期において、できるだけ予定よりも先行させておく必要があります。
出来高累計曲線の長所は、作業の進捗度合がわかりやすく、予定工程曲線と実施工程曲線を比較できるので、適切に工程管理が行えること です。一方、短所は必要な日数、工期に影響する作業がわからないことです。
出来高累計曲線の作成手順は、次のとおりです。
- バーチャートを作成します。
- 各部分工事(種別)工事費構成比率を求めます。
( 部分工事費 / 全工事費 ) × 100 = 工事費構成比率(%) - 月ごとの部分工事別予定出来高に工事費構成比率を乗じて、全体工事に対する予定出来高比率を求め、これを累計して全体工事の予定出来高累計曲線を求めます。
- 工事の進捗にしたがって、定期的に実績を調査のうえ、上記手順により実施曲線を記入し、予定と実施との両曲線を比較して遅延の有無を調べ、工程を管理します。
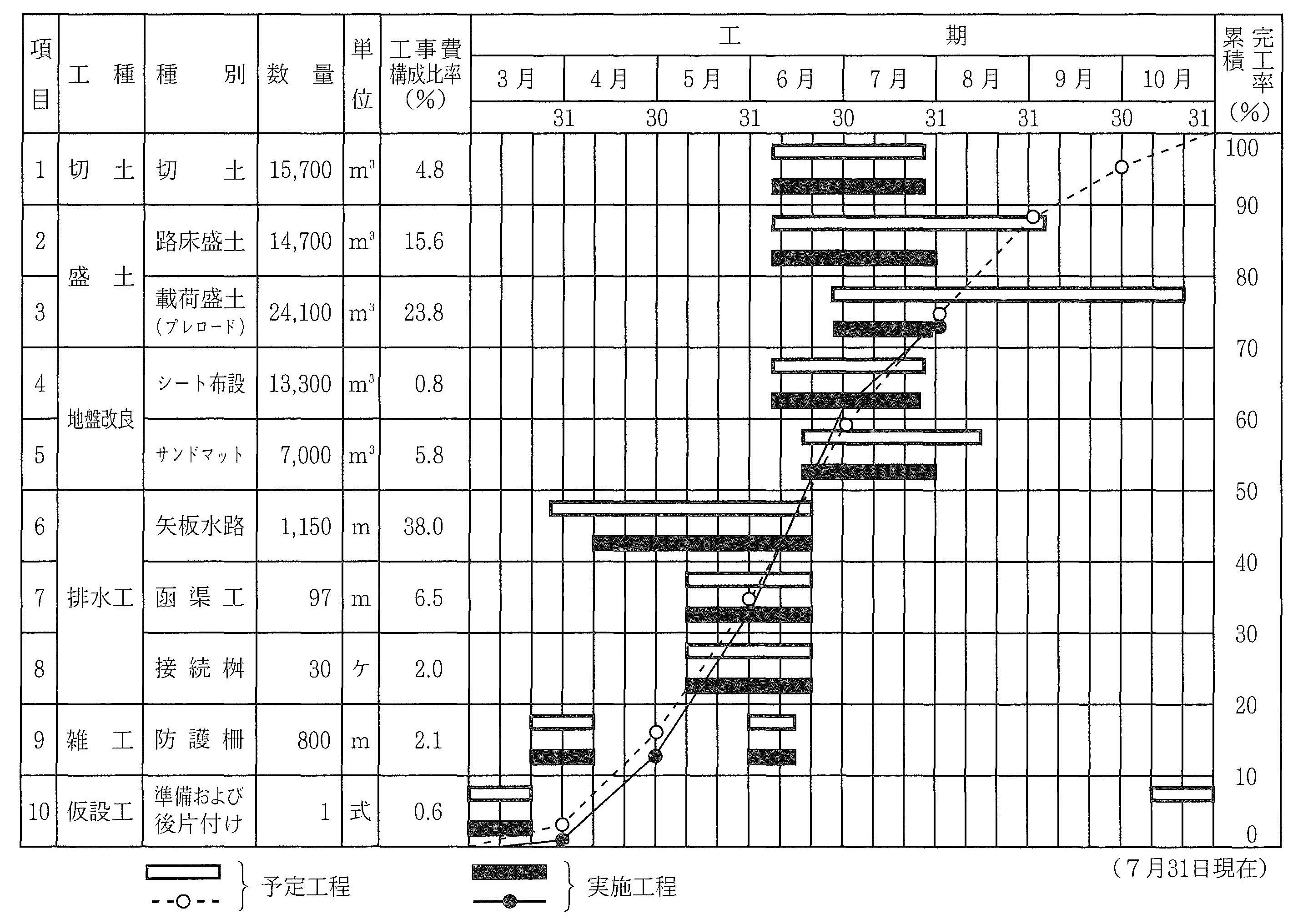
図-10:パーチャートに出来高累計曲線を加えた例
工程管理曲線
工程管理曲線(バナナ曲線)は、アメリカのカリフォルニア州道路局で、代表的な道路工事についての工程曲線を作成して、時間的経過と出来高との関係を調査研究し、道路工事の工程管理曲線としたものです。この曲線は、時間の経過について出来高工程の上下変動域を調べたもので、2つの曲線がバナナの形をしているところからバナナ曲線と呼ばれています。予定工程は平均施工速度をもとに作成されるが、実績曲線は工事に関係する種々の条件により、予定工程との間にずれが生じます。このずれが許容可能な範囲であるか否かの判定に、このバナナ曲線が用いられます。
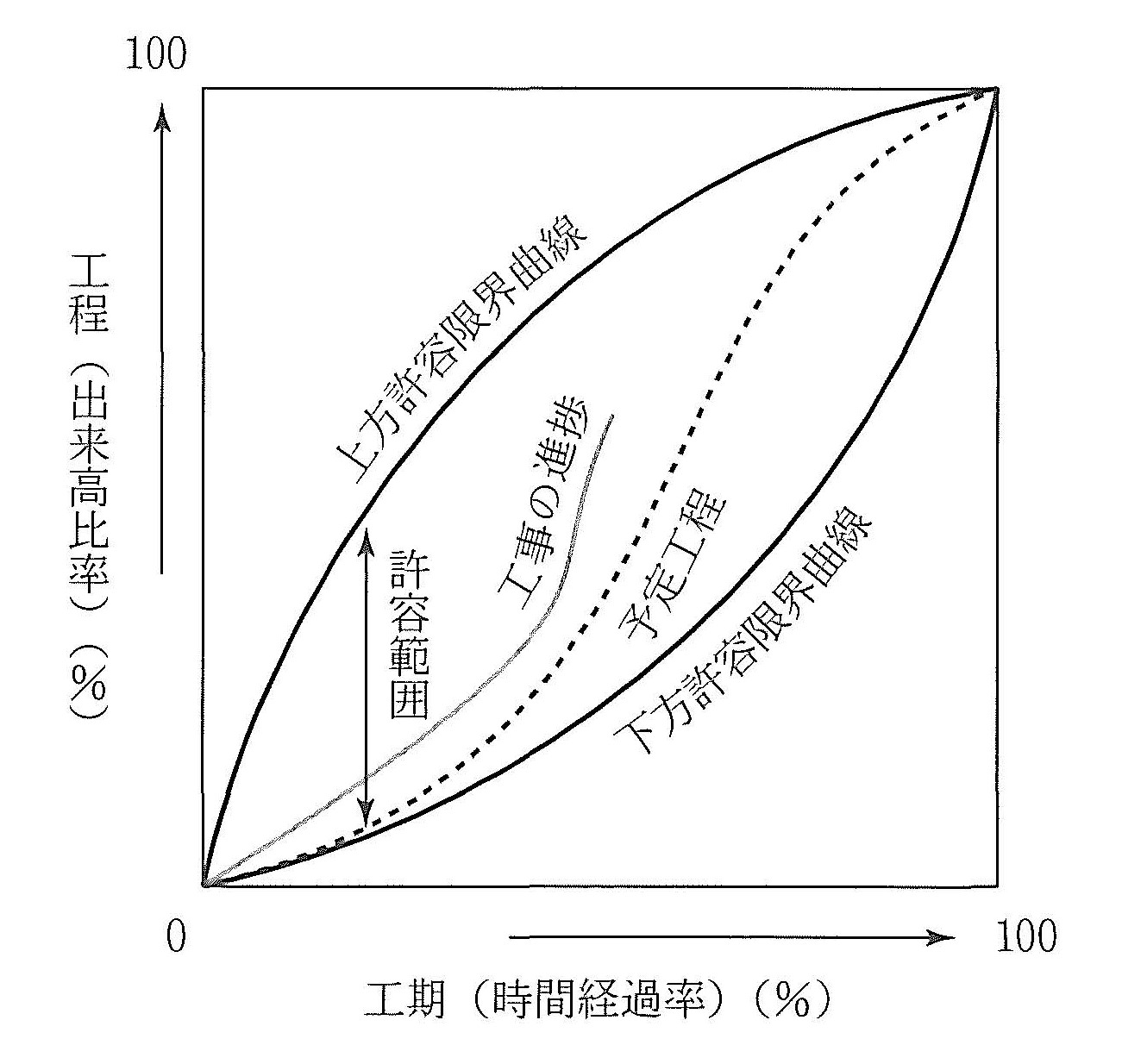
図-11:工程管理曲線(バナナ曲線)
工事開始時点をOとし、終了時点(工期)を100%として、時間(日数)経過率に応じたその工事の出来高(%)をプロットして、出来高が上方許容限界曲線と下方許容限界曲線の間にあればよい。出来高が下方許容限界曲線の下にあると、工程進捗が遅れていることがわかり、緊急に対策が必要となります。また、上方許容限界曲線の上にある場合は、人員や機械の配置が多すぎるなど、計画に誤りがあることが考えられるので、やはり検討を必要とすることになります。
工程管理曲線(バナナ曲線)は、総出来高金額による管理ですので、作業の進捗度合がわかりやすいが、一方、作業の手順が不明確で、作業に必要な日数や工期に影響する作業がつかみにくいというデメリットもあります。
工程管理曲線(バナナ曲線)の計画および管理の方法を要約すると、次のとおりです。
- 横線式工程表に基づいて予定工程曲線を作成し、それが管理曲線の許容限界内、例えば、バナナ曲線の中に入るかどうかを検討します。
- 予定工程曲線が許容限界から外れるときは、一般に不合理な工程計画と認められるため、再検討のうえ横線式工程表の主工事の位置を変更して、予定工程曲線がバナナ曲線の許容限界内に入るように調整して計画しなおします。
- 実施工程曲線がバナナ曲線の上方許容限界を越えたときは、工程が進み過ぎているので、必要以上に大型の機械を入れるなど不経 済になっていないか検討します。
- バナナ曲線の下方許容限界を実施工程曲線が下回るときは、工程遅延は致命的であり、突貫工事が不可避であるため、突貫工事に対して最も経済的な実施方策を根本的に検討することが必要となります。
5 ネットワーク式工程表
ネットワーク式工程表は、多種の作業の中でどれが全体工程に最も影響するかを知り、あらかじめ管理の重点となる作業を決定するため、また、工程遅延を防止し適切な措置を行う場合に、どの作業をどの程度早めたらよいかを的確に判断するために開発され、利用されてきたものです。
長所
ネットワーク式工程表の長所は、作業の順序関係が明確になり、施工計画の段階で作業手順の検討がつくされ、その全体の姿が担当者の頭に入ります。工程のネックとなる作業が明らかになるので、重点管理が可能になります。作業順序がはっきりするため、工事担当者間で細部にわたっての具体的な情報伝達ができます。工事途中での天候や段取替えなどで当初計画を変更せざるを得ない場合、速やかに対処できます。複雑な仕事でも、コンピュータの利用によって、短時間に工程計画ができます。
短所
ネットワーク式工程表の短所は、ネットワークを構成する各作業の歩掛りが正しくなければ、全体の精度が悪くなります。横線式工程表に比べて、工程表の作成に費用と労力を要します。横線式工程表に比べて、より多くのデータを必要とします。修正が比較的むずかしいです。
ネットワーク式工程表を用いた工程管理手法は、大別して以下のように分けられます。
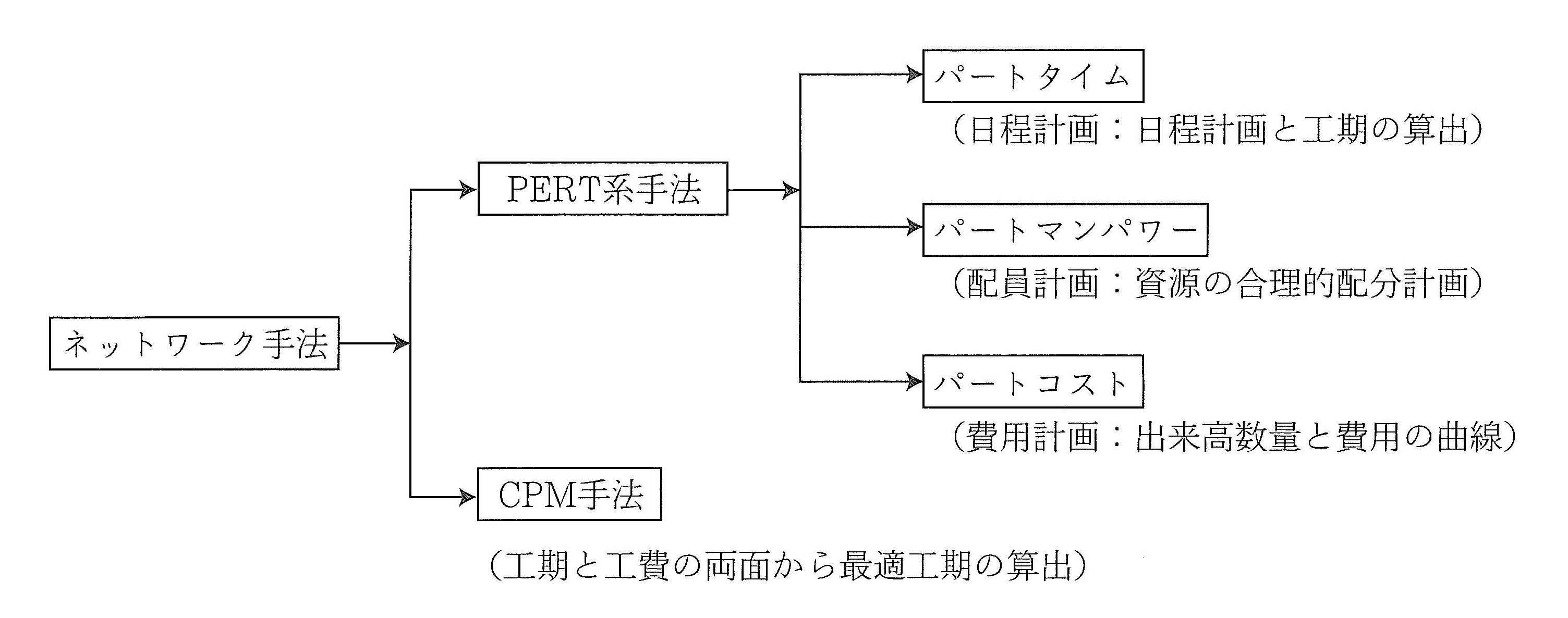
図-12:ネットワーク手法の分類
- PERT系手法(Program Evaluation and Review Technique)
- 日程計画(パートタイム):時間の要素を中心として、工期や各作業の開始・終了を求めていく手法。
- 配員計画(パートマンパワー):日程計算に基づいて各作業の所要資源数量を出し、山積み計算を行います。その後、必要資源が日ごと凹凸がないように、各作業の着手時期を山崩し計算を用いて調整する手法。
- 費用計画(パートコスト):工程計画により、各作業の出来高数量に単価を乗じ、その結果を累計することにより、出来高数量と費用に関する累計曲線を求める手法。
- CPM手法(Critical Path Method)
- 時間を費用との関連においてとらえ、工期を短縮するにつれて費用がどのように増加していくかをみながら、最適工期、最適費用を設定する手法。
基本的考え方
ネットワーク式工程表作成の基本的考え方は、ネットワーク手法の基本的ルール、まる(○)と矢線(→)の結びつきで表現でき、かつ目的に対して弾力的に表示可能なものです。
作成の前提の第ーは、ネットワーク式工程表作成の目的を明確にとらえることです。一般には、
- 経済的スピードで工期を守る
- 有効な資機材の配分計画
- 工費(労務費、材料費)の節減
- 経費の節減
- 資機材、人員の合理的運営
に主眼をおいています。
最近の工事では、さらに複雑な要素が絡み合い、多くの問題を含んでいることも多くなっています。
第二として、ネットワーク式工程表作成の要点を以下に示します。
- 目的(仕事の目的)
- 対象(何について)
- 範囲(どこからどこまで)
- 相手(折衝)
- 工法(技術的に最適な工法)
- 工期(いつからいつまで〉
- 費用(機材費、労務費、経費)
これらは各人が業務を遂行する場合、あるいはマネージメントとして管理する場合の基本的態度にほかなりません。
ネットワーク式工程表の作成手順
基本用語
1 作業(アクティビティ)
- 作業は、矢線(→)で示されます。
- 矢線の長さは、時間には無関係で、形は任意でよろしいです。
- 矢線の尾が作業開始、頭が作業終了を示します。
- 一般的に、作業の所要時間を矢線の下に書き、作業名または作業内容を上に書きます。

図-13:作業(アクティビティ)
2 イベント(結合点)
イベントは、〇で示し、○の中に0または正整数を書き込み、これをイベント番号と呼びます。工程表では、作業の前後関係(次作業の開始条件となる前作業の完了)を明らかにする役割を持ちます。
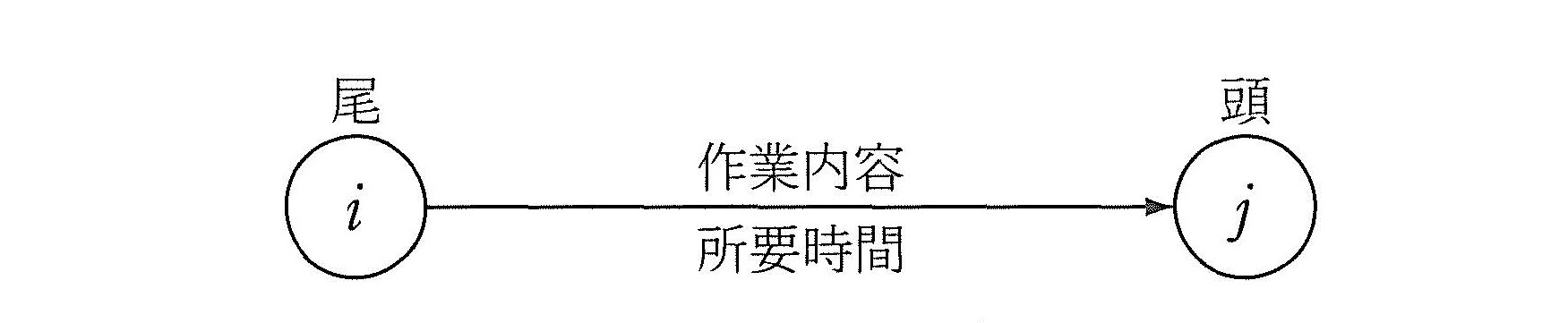
図-14:イベント(結合点)
3 ダミー(疑似作業)
ダミーは、同一の作業が複数発生する場合に、起終点のイベントを区別するために使われる所要時間ゼロの疑似作業です。点線の矢印で表記します。
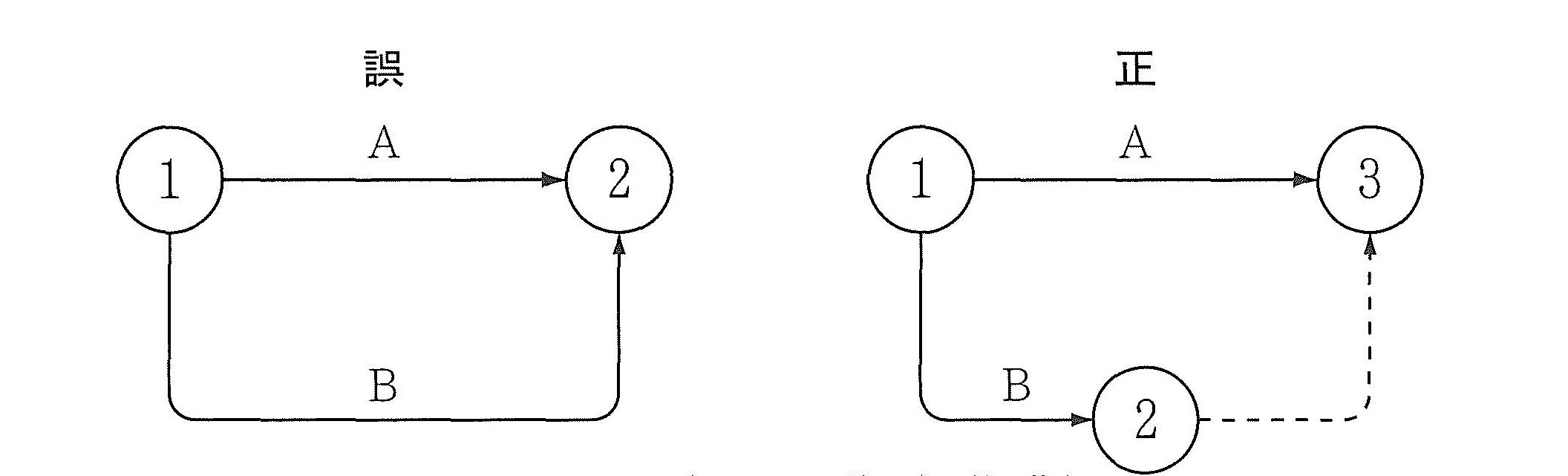
図-15:ダミー(疑似作業)
4 所要時間
作業の開始から終了までに要する時間を所要時間といいます。建設工事では、一般に日を単位としています。
基本ルール
1 先行作業と後続作業
ある結合点において、入ってくる矢線(先行作業B、C)がすべて完了した後でなければ、結合点から出る矢線(後続作業D)は開始できません。
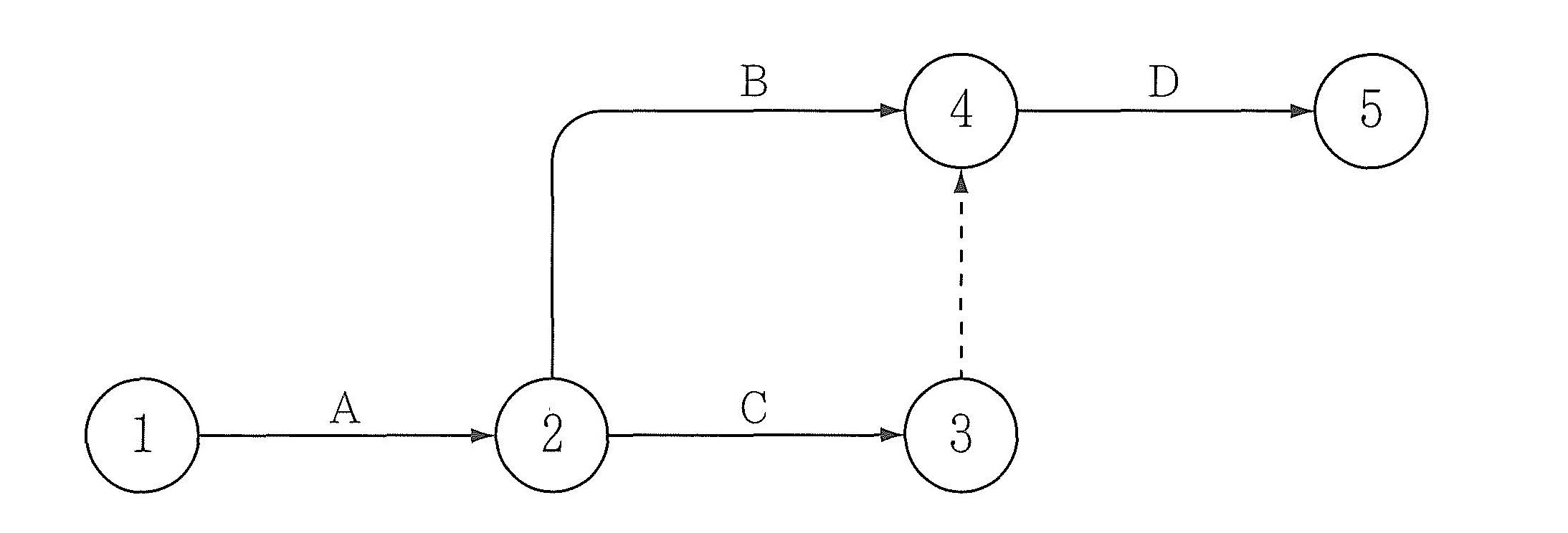
図-16:先行作業と後続作業
2 イベント(結合点)番号
イベント番号は、同じ番号が2つ以上あってはなりません。